The three main components of an x-ray CT system are the x-ray source, rotary table and detector. Different CT system configurations exist: for example, flat panel detectors (DDA) or linear diode array detectors (LDA) can be used.
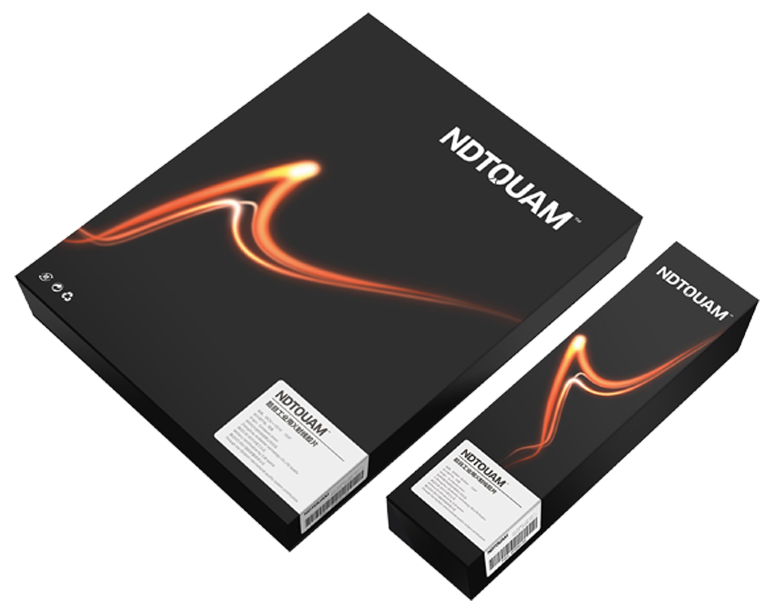
With LDAs the phenomenon of x-rays scattering, relevant while scanning high density materials as in aerospace applications, does not impact the scan. However longer scanning times are required.
The x-ray source-to-detector distance and x-ray source-to-object distance define the geometrical magnification of the CT scan and the voxel size of the 3D CT model of the part. The use of variable X-ray source-to-detector distances, as offered in the NSI system portfolio, is also fundamental for aerospace applications to achieve the best signal possible.
CT technology is based on x-ray’s attenuation principles. The size and the thickness of the part and the material density therefore plays a fundamental role in its effective use. The larger the component and the denser the material, the more power is required for the x-rays to penetrate.
The output of a CT scan is a 3D model of the part, upon which it is possible to perform very accurate measurements without any form of contact or need to cut or destroy the part. CT also allows for material inspection and identification of internal defects such as voids, cracks, etc. When inspecting composite materials, CT can also be used to identify delaminations.
-
Sales@hata-ndt.com
-
0086-0371-86172891