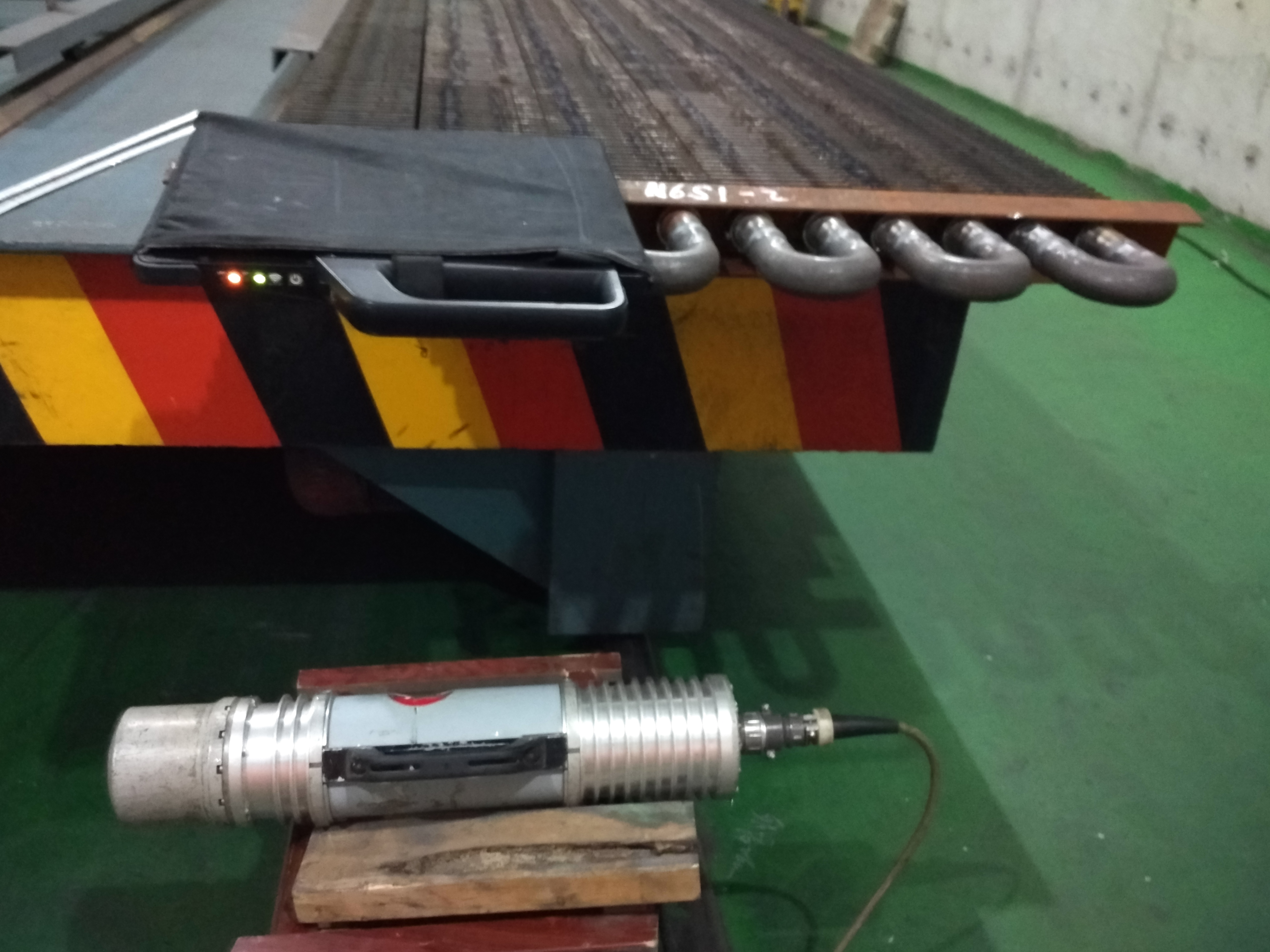
Austenitic stainless steel is one of the most widely used metal materials in petrochemical production. Its welding performance is good, but it is also prone to many problems in the welding process, mainly in the following:
1. Intergranular corrosion
Austenitic stainless steel welded parts are prone to intergranular corrosion at the welded joints. According to the theory of lean chromium, the reason is that the welds and heat effects during welding are kept at a joint temperature of 450~850 °C for a certain period of time. High chromium carbide (Cr23C6) is precipitated at the boundary, causing the chromium content in the surface layer of the crystal to decrease, forming a chromium-depleted region. Under the action of the corrosive medium, the chromium-depleted region of the grain surface is corroded to form intergranular corrosion. There is no obvious change in the surface of the corroded welded joint. When the force is applied, it will break along the grain boundary and almost completely lose strength.
In order to prevent and reduce intergranular corrosion at the welded joint, the general preventive measures are
(1) Use low-carbon or ultra-low-carbon welding consumables, such as A002, or use welding rods containing stabilizing elements such as titanium and niobium, such as A137, A132, etc;
(2) A certain amount of ferrite forming element is melted into the weld by the welding wire or the welding rod, so that the weld metal becomes a two-phase structure of austenite + ferrite (ferrite generally controls 4-12%);
(3) Reduce the overheating of the weld pool, select a smaller welding current and a faster welding speed to accelerate the cooling rate;
(4) Post-weld stabilization annealing treatment of weldments with high resistance to intergranular corrosion resistance.
2 . Welding hot crack
The main reason for the occurrence of hot cracks is that the dendrites in the weld are strong in orientation, which is conducive to the formation and aggregation of low-melting eutectic products of elements such as S and P. In addition, such steel has a small thermal conductivity (about 1/3 of low carbon steel), a large coefficient of linear expansion (50% larger than that of low carbon steel), so the welding stress is also large, and furniture generates hot cracks. The way to prevent it is:
(1) Select a welding material with a low carbon content, and use a welding material containing an appropriate amount of elements such as Mo and Si to form a two-phase structure of austenite and ferrite, thereby reducing segregation;
(2) Try to use high-quality welding rods of alkaline coatings to limit the content of S, P, C, etc. in the weld metal.
3. Stress corrosion cracking Stress corrosion cracking is the delayed cracking of welded joints subjected to tensile stress in a specific corrosive environment. The stress corrosion cracking of austenitic stainless steel welded joints is a serious failure mode, which is characterized by brittle failure without plastic deformation.
Stress corrosion cracking prevention measures:
(1) Adopt a proper welding process to ensure that the weld is well formed without any stress concentration or pitting defects, such as undercuts; take a reasonable welding sequence to reduce the residual stress level of the weld;
(2) Reasonable selection of welding consumables, welds and base metals should have a good match, without any bad microstructure, such as grain coarsening and hard brittle martensite.
(3) Stress-relieving treatment: post-weld heat treatment, such as complete annealing after welding, using post-weld hammering or shot peening when it is difficult to perform heat treatment. 4. Low temperature embrittlement of weld metal
4 . For austenitic stainless steel welded joints, the plastic toughness of the weld metal is a key issue when used at low temperatures. At this time, the presence of ferrite in the weld bead always deteriorates the low temperature toughness. It is generally possible to prevent the low temperature catalysis of the weld metal by selecting a pure austenitic weld and adjusting the welding process to obtain a single austenitic weld.
5. σ phase embrittlement of welded joints After the weldment is heated for a certain period of time, a brittle σ phase is precipitated in the weld, resulting in embrittlement of the joint and a significant decrease in ductility and toughness. The precipitation temperature range of the Σ phase is 650-850 ° C. During the high temperature heating process, the σ phase is mainly transformed from ferrite. The longer the heating time, the more the σ phase precipitates.
Preventive measures:
(1) Limiting the ferrite content (less than 15%) in the weld metal, using superalloyed welding materials, ie high nickel welding consumables;
(2) Adopt a small range to reduce the residence time of the weld metal at high temperatures;
(3) The precipitated σ phase is subjected to solution treatment when conditions permit, and the σ phase is dissolved into austenite.
-
Sales@hata-ndt.com
-
0086-0371-86172891