Because the boiler needs to withstand higher temperatures and pressures during use, it is easy to explode, threatening the safety of the society, enterprises and employees, and life safety. Therefore, the boiler is strengthened during the manufacturing phase, installation phase and use phase. Detection has important practical significance.
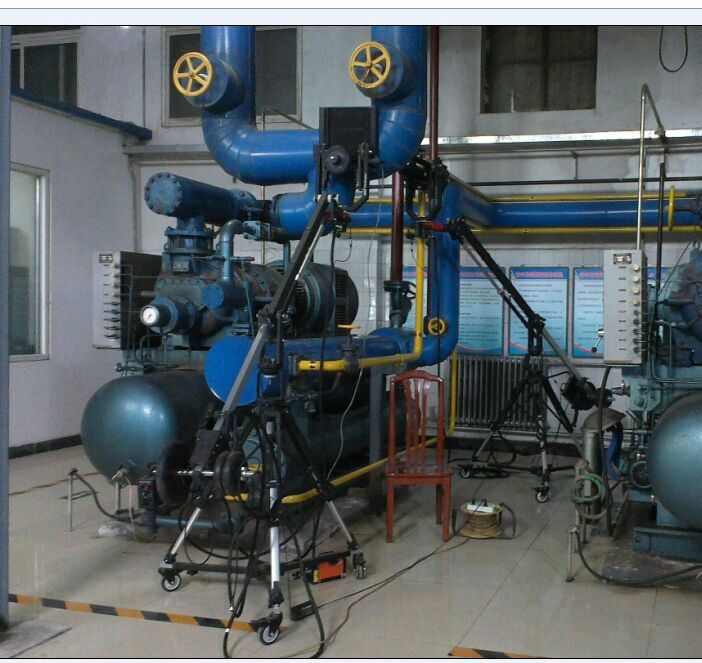
Boiler detection method
Weld inspection is an important part of non-destructive testing of boilers due to frequent boiler problems in welded parts. Non-destructive testing methods commonly used in boilers include visual inspection, surface inspection, magnetic particle inspection, ultrasonic inspection, and radiation inspection. Visual inspection is often used to detect situations where defects are more pronounced. Radiographic and surface inspection methods are commonly used to test flat butt welds and girth welds. For butt welds, single wall transmission is typically used. Please note that the focal length, voltage and exposure are determined. The detection can be either a single wall or a double layer. Magnetic particle detection methods are generally used in the presence of cracks. Non-destructive testing using ultrasonic waves is also a common method for detecting thick-walled welds and other conditions that cannot be detected by radiation.
Boilers play a very important role in daily life, and many industries use boilers. Due to many factors in the operation process, the boiler will have a series of failure problems. In this regard, in order to enable the boiler to operate safely and steadily, it is necessary to pay attention to the boiler inspection work. Only with reasonable detection technology can the boiler be discovered and handled in time. The traditional detection technology can detect the failure of the boiler to a certain extent, but the detection effect is not satisfactory.
-
Sales@hata-ndt.com
-
0086-0371-86172891