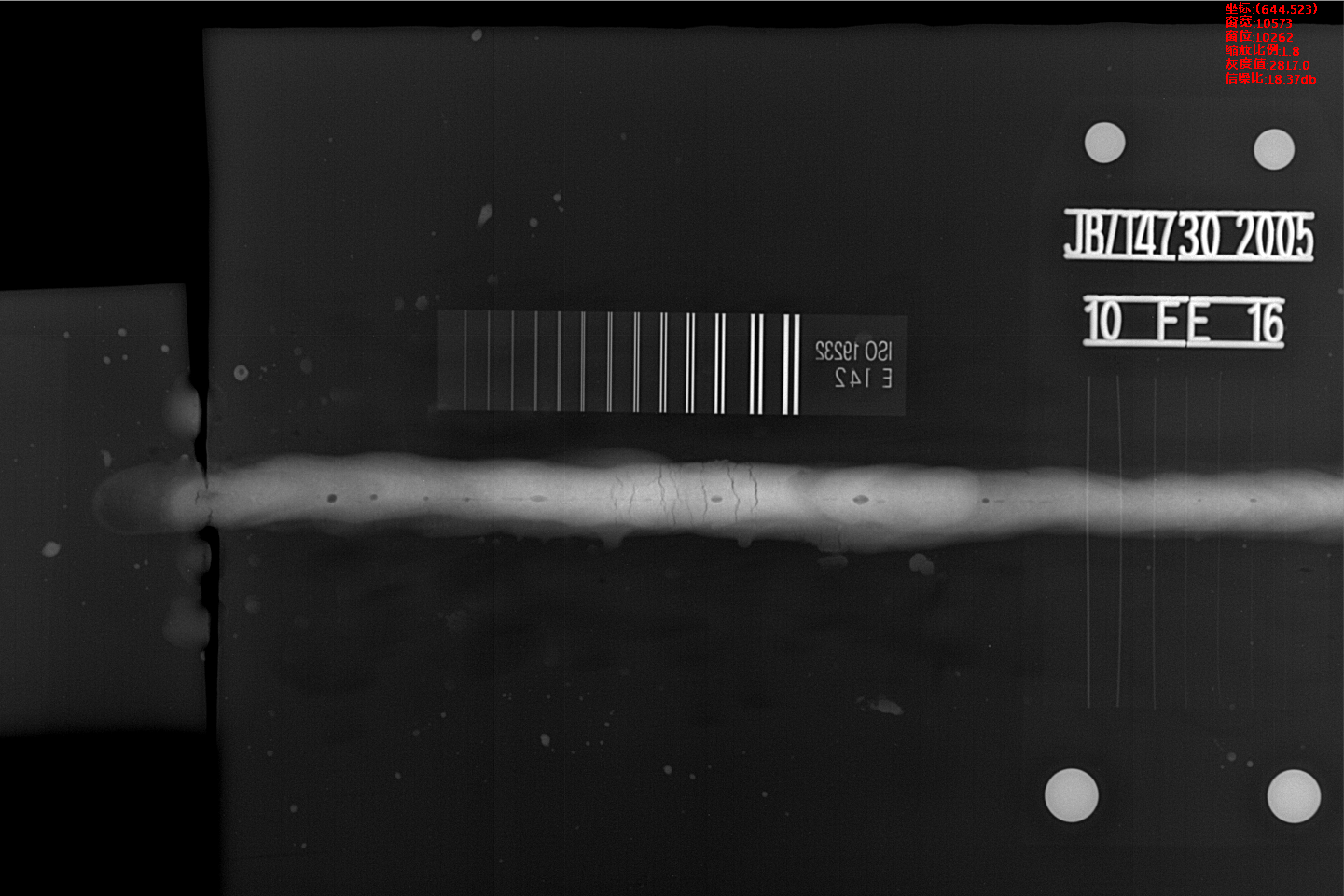
Magnetic particle detection sensitivity
1. Definition: The smallest size of the defect found
2. Sensitivity test piece: It is mainly used to test system sensitivity and verify the comprehensive performance of magnetic particle testing equipment, magnetic powder and magnetic suspension. Standard test strips are used for continuous magnetization and cannot be used for residual magnetization.
3. Sensitivity classification: high, medium and low. For example, the thickness of the A-type test piece is 50um, the high sensitivity is the artificial groove depth of 7um; the medium sensitivity is the artificial groove depth of 15um; the low sensitivity is the human engineering depth of 30um.
4. Place the test piece: see the smooth surface, that is, the grooved surface is opposite to the surface of the workpiece. Use a transparent tape (thickness should be less than 100um) when fixing the test piece. The tape cannot cover the artificial defect.
Classification of magnetic marks
1. Magnetic mark display is divided into related display, non-related display and pseudo display
2. Magnetic marks with a ratio of length to width greater than 3, treated by strip magnetic marks; magnetic marks with an aspect ratio of not more than 3, treated by circular magnetic marks.
3. Magnetic traces less than 0.5mm in length do not count
4. When two or more magnetic marks are on the same straight line and the spacing is not more than 2mm, it is treated by a magnetic mark, and the length is the sum of the two magnetic marks plus the spacing.
5. When the angle between the defect and the workpiece of the workpiece (shaft or tube) axis or busbar is greater than or equal to 30°, it shall be treated according to the lateral defect and the other shall be treated according to the total line defect.
Observation of defect magnetic marks
1. The observation of the defect magnetic mark should be performed immediately after the formation of the magnetic mark.
For the detection of non-fluorescent magnetic powder: the evaluation of the defect magnetic mark should be carried out under visible light, and the visible light illumination of the workpiece surface should be ≥1000lx; when the scene cannot be satisfied due to the condition, the visible light illumination should not be lower than 500lx.
For the detection of fluorescent magnetic powder: the irradiance of the black light on the surface of the workpiece is ≥1000uW/cm2, and the wavelength should be in the range of 320nm-400nm. Observe the display of the fluorescent magnetic powder, and the inspection personnel are not allowed to wear glasses that have an influence on the detection.
2. Evaluation of the defect magnetization display: it should be in the dark room or in the dark (the visible light illumination is not more than 20lx). The tester enters the dark area and adapts to the darkness for at least 3 minutes.
3. In addition to confirming that the magnetic trace is caused by local magnetic unevenness or improper operation of the workpiece material, other magnetic trace displays should be treated as defects. When identifying small magnetic marks, use a 2-10 magnification magnifying glass to observe.
-
Sales@hata-ndt.com
-
0086-0371-86172891