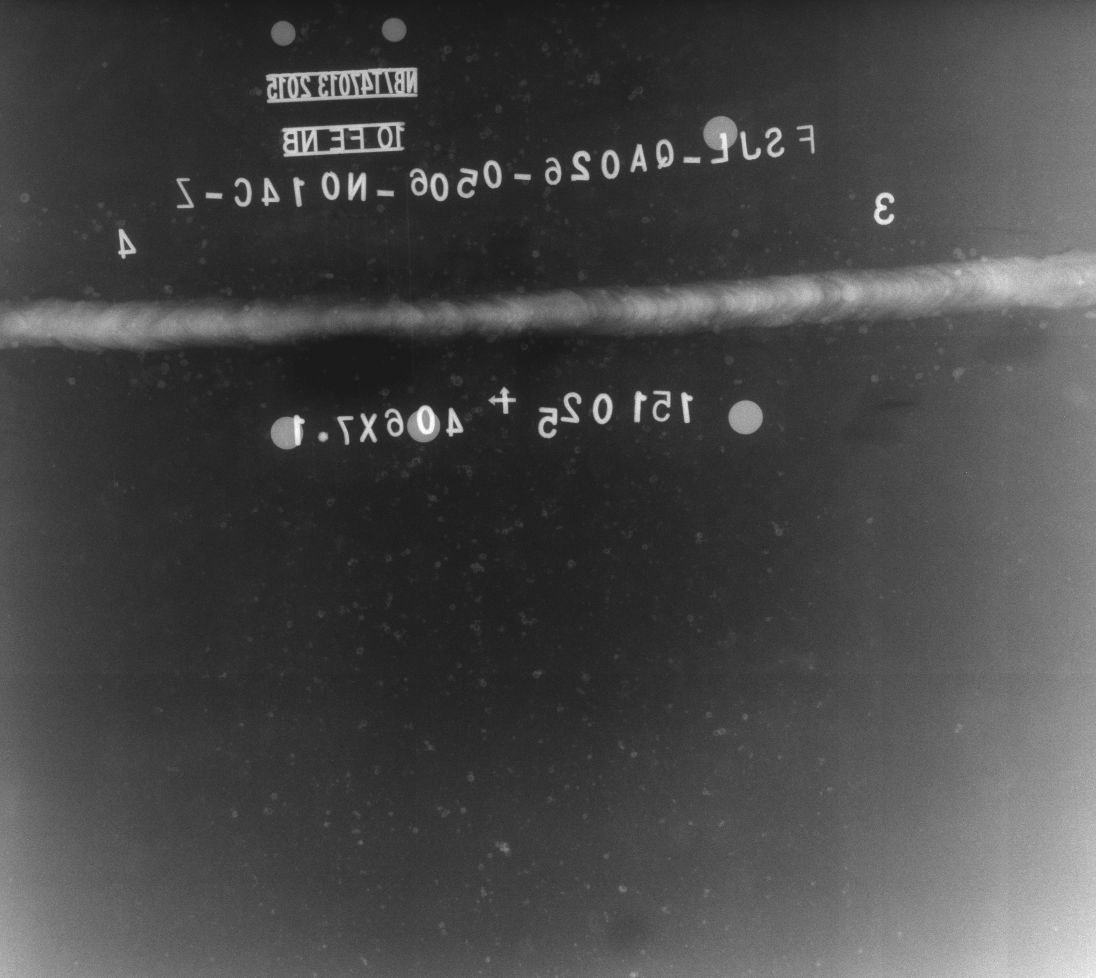
1. Ultrasonic testing
Weld quality Ultrasonic testing is mainly used to detect internal defects in welded joints, such as pores, slag inclusions, unwelded heads, unfused, cracks and other welding defects. Ultrasonic waves have a higher detection rate than ray-like defects such as cracks and unfused in welds.
Conventional ultrasonic testing does not present a hazard to the human body. It can provide depth information of the defect and an area-type defect perpendicular to the incident direction of the ray that is easily leaky. Instant results; complementary to radiation detection.
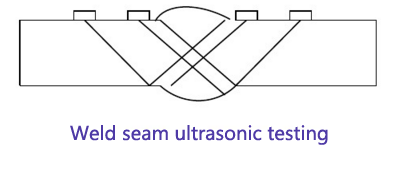
2. Characteristics of ultrasonic testing
(1) Area type defect detection rate is high, volume type detection rate is low
(2) Suitable for detecting workpieces with large thickness
(3) Suitable for testing various test pieces
(4) Low inspection cost, fast speed and small instrument size
(5) Invisible images of defects cannot be obtained, qualitative difficulty, and quantitative accuracy is not high
(6) No direct witness record of test results
(7) Accurate positioning of defects in the thickness direction of the workpiece
(8) Material and grain size have an impact on flaw detection
(9) Irregular shape of the workpiece and some structures will affect the detection
(10) Uneven or rough surfaces can affect coupling and scanning, thus affecting detection accuracy and reliability
Common standards for weld ultrasonic testing GB/T11345-2013 "Non-destructive testing of welds, ultrasonic testing technology, inspection grade and assessment" (implemented on June 1, 2014, replacing the original GB/T11345-1989 "manual ultrasonic flaw detection method for steel
welds and classification of flaw detection results"), GB/T29712-2013 "Non-destructive testing of welds for non-destructive testing", GB/T29711-2013 "Non-destructive testing of welds by ultrasonic testing of welds in the welds" JB/T4730.3-2005 "Non-destructive testing of pressure equipment" - Part 3
Suitable for ultrasonic testing of butt welded joints with a thickness of 8mm-400mm for the base metal. Ultrasonic testing of butt welded joints with a base metal thickness of 6 mm to 8 mm shall be carried out in accordance with the provisions of Appendix G (Normative). Ultrasonic testing of supports, structural members and spiral welded joints of boilers, pressure vessels and pressure piping may also be carried out in accordance with the provisions of this regulation. Reference for ultrasonic testing of butt welded joints of titanium pressure vessels
Applicable to boiler, pressure vessel and pressure pipe circumferential welded joints with wall thickness greater than or equal to 4mm and outer diameter of 32mm.
It is not suitable for ultrasonic testing of cast steel welded joints, steel pipe butt welded joints with outer diameter 159mm, and fillet welds with inner diameter less than or equal to 20mm. It is also not suitable for outer diameter less than 250mm or the ratio of inner and outer diameter is less than Ultrasonic testing of 80% longitudinal welded joints. Not suitable for ultrasonic testing of cast steel, austenitic stainless steel boilers, pressure vessel tubes and pressure piping to very hung joints.
-
Sales@hata-ndt.com
-
0086-0371-86172891