There are many practical applications of weld inspection using eddy current techniques. These include the following:
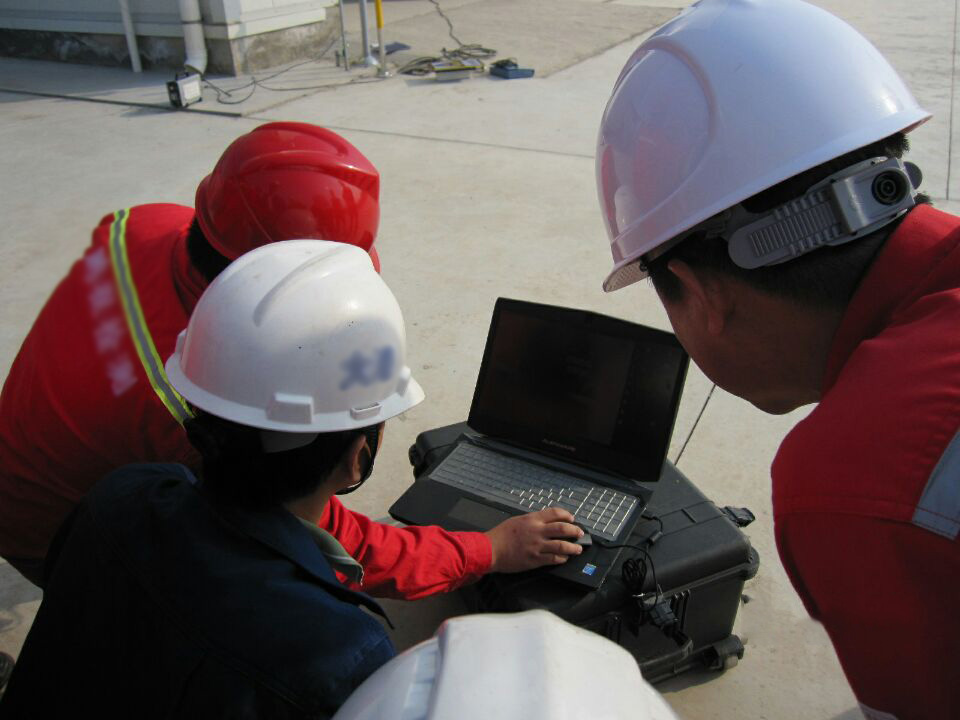
Offshore structures.
By far the widest use of eddy current weld inspection occurs in the offshore industry. Offshore structures such as drilling platforms are subjected to cyclical loads twice daily (tides) and, more unpredictably, by severe weather. Fatigue crack propagation can occur topside or underwater and periodic inspection of critical weld areas is required. Frequently, topside inspections are only possible by rope access. Underwater inspections and repairs are often done by divers at acceptable depths and in acceptable water environments. At more extreme depths in cold water areas, remote operated vehicles (ROVs) have been developed to carry out surface preparation, eddy current weld inspection, weld repair, and repair inspection in one unit.
Bridges, cranes, traffic signals.
All of these structures are subject to cyclical loading on their welded structures, as well as weather-related loading and weight loading in cranes and bridges. Cantilevered traffic arms are a relatively recent application that has resulted from the failure of such arms because of weather-induced weld fatigue. Such failures have had fatal results.
Ships.
Ships are subject to bending and torsional moments in day-to-day use. Extreme weather conditions, shifting loads, and grounding can lead to extreme loading of the superstructure and overstress critical welded joints.
Submarines.
Eddy current is often used in the inspection of new welds and for the detection of fatigue cracks in welded joints. Submarines are subject to the same loading as surface ships plus have the added stress of the cyclical loading that accompanies pressure changes associated with submerged operations.
Amusement park rides.
Another relatively recent application is the inspection of amusement park rides. Again, these rides are subject to the same cyclical loading as bridges and cranes. Due to public demand, theme parks in warmer climates are often required to be in operation 364 days a year. Every day a ride is unavailable due to maintenance closure a negative public reation is encountered, even if the closure is for safety-critical inspection and maintenance. Eddy current techniques for the inspection of track and cars represent a significant reduction in manpower and downtime, resulting in more cost-effective and higher quality maintenance and inspection along with more paying hours of operational attractions.
Law enforcement.
Among the more unconventional uses for eddy current weld inspection are law enforcement applications. The technique can be used to identify welded joints in automobiles where you would not expect to find them. So called "cut and shut" welds across a vehicle's chassis can easily be detected using eddy current technology as well as the welded area surrounding false VIN plates. This can be done without damage to the paintwork on the vehicle being inspected. Also, specially designed probes have been used to detect the removal of material from prison bars in penal institutions. However well the cut is hidden with dirt, shoe polish, or paint, the eddy current technique will ignore the filler material and detect the cut in the bar.
Rotary eddy current techniques.
Special rotary probes were developed to aid in the inspection of welded steel engineering structures after the Kobe earthquake to allow construction engineers to evaluate structures that were under construction during the quake. Rotary techniques can detect flaws in any orientation, allowing the contractor to assess quickly whether cracks in the welds had occurred and to effect repair or demolition as necessary.
-
Sales@hata-ndt.com
-
0086-0371-86172891