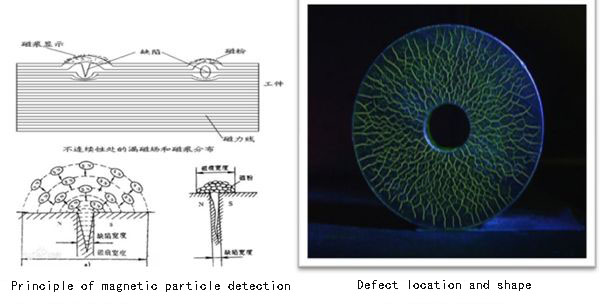
Magnetic particle detection is to magnetize (integral magnetization or local magnetization) by applying a magnetic field to the workpiece to be inspected, and a magnetic field line will escape from the surface of the workpiece at the surface and near surface defects of the workpiece to form a leakage magnetic field, which can be adsorbed by the presence of magnetic poles. The magnetic powder applied on the surface of the workpiece forms an aggregated magnetic mark, thereby showing the presence of defects. Magnetic particle testing methods are widely used to detect defects on the surface or near surface of magnetic materials. Used to detect welds, castings or forgings such as valves, pumps, compressor components, flanges, nozzles and similar equipment. To detect defects on a deeper inner surface, a radiographic or ultrasonic test is required.
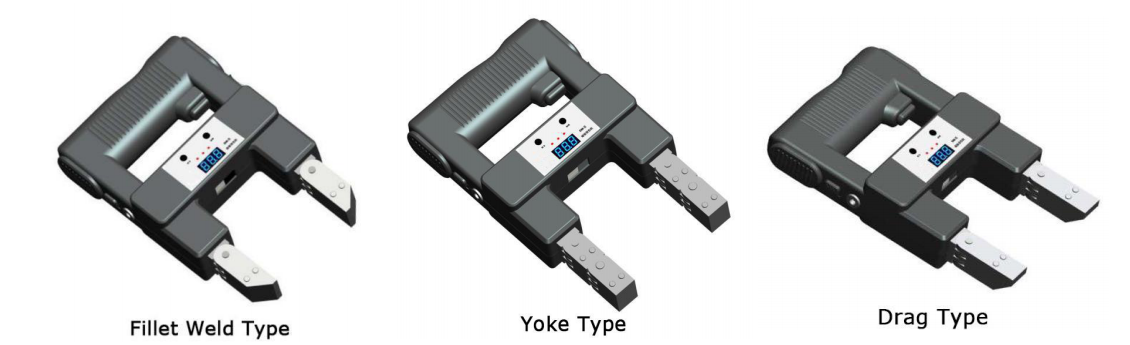
The yoke is one of the commonly used tools for magnetic particle inspection. At present, ordinary yokes (external power supply and lighting) on the market have relatively limited limitations, and outdoor work is troublesome, so the wireless yoke is born. He has built-in power and lighting (white light and black light), no external power supply and lighting, and solves a lot of troubles for outdoor work. It is small in size and light in weight, and it is convenient to carry out work. Most importantly, he can not only detect surface defects. It can also detect defects within 3mm depth; in addition, his endurance is also very good, can work for two days or so when fully charged.
One of the latest yokes, based on the yoke described above, uses a new magnetization method to ensure surface detection sensitivity and deep burying defects, with a detection depth of 3 mm; and with three different probes for multiple purposes, Suitable for inspection of various occasions and workpieces.
-
Sales@hata-ndt.com
-
0086-0371-86172891