Wire rope or cable is made by weaving many individual wires together to produce a product that is both strong and flexible. Wire rope is used in many safety critical applications in addition to chair lift and gondola systems. Some of these applications include hoisting systems, such as cranes and winches; guy wires used in tall antennas and towers; and mooring lines of oil drilling platforms at sea. A cable failure in one of these applications could have very serious consequences.
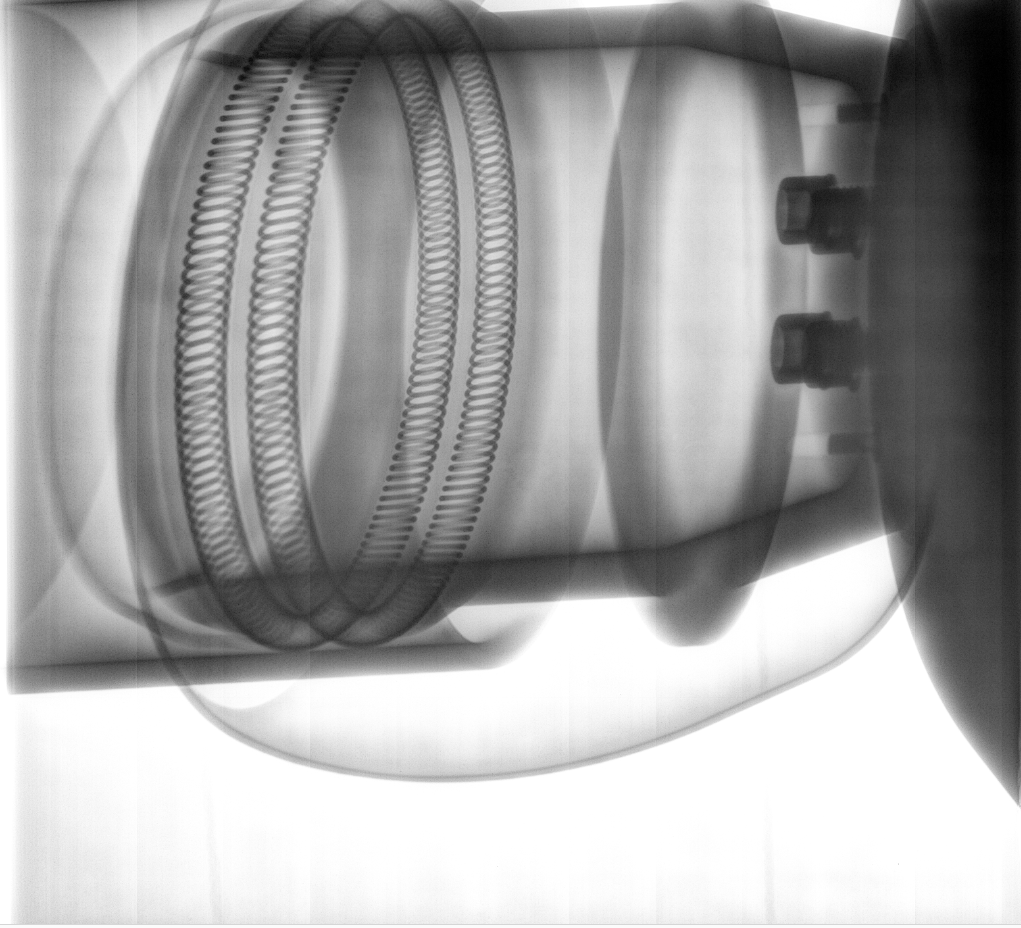
All wire rope eventually wears out making periodic inspections necessary throughout the service life of the rope. Wire rope is prone to damage and wear due to abrasion, fatigue, corrosion, and improper handling. NDT personnel look for localized flaws or loss of metallic cross-sectional area using a variety of inspection methods. The least sophisticated method is visual inspection. Inspector simply look for broken strands, wear and corrosion on the surface of the cable. However, for a more thorough evaluation, a number of instruments have been developed that allow inspectors to assess the internal areas of the cable.
One of the more widely used of these instruments uses magnetism to inspect the rope. The inspection instrument is placed around the wire rope and moved along the rope or the rope is pulled through the instrument. Strong permanent magnets or electromagnets are used to create a strong magnetic field within the rope. The rope is said to be magnetically saturated because it is caring all the magnet flux that it possibly can. In areas where the rope is damaged, it can not support as much of the magnet flux and some of it "leaks" out of the rope. Sensors in the inspection head detect the magnetic flux leakage caused by the internal or external defects in the rope. Defects as small as 0.05 % of the rope's cross-sectional area can often be detected.
-
Sales@hata-ndt.com
-
0086-0371-86172891