Magnetic particle inspection and magnetic detection
Leakage magnetic field flaw detection: After magnetization of ferromagnetic material or workpiece, if there is discontinuity on the surface and near surface (the homogeneity of the material is damaged), the magnetic field lines leave the workpiece and enter the workpiece at the discontinuity. Local distortion occurs on the surface to generate magnetic poles, and a detectable leakage magnetic field is formed for flaw detection.
Leakage magnetic field detection includes magnetic particle inspection and detection of leakage magnetic fields using a detecting element. The difference is:
This wind flaw detection utilizes a ferromagnetic powder-magnetic powder as a magnetic field sensor, that is, a magnetic field which is adsorbed at a discontinuity by a leakage magnetic field is aggregated to form a magnetic mark, thereby exhibiting a position, a shape and a size of discontinuity.
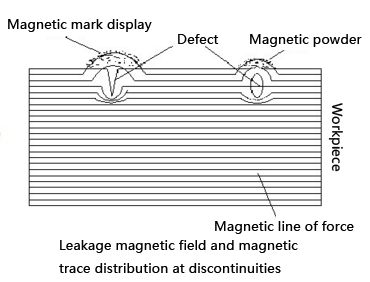
Magnetic field sensors that detect a leakage magnetic field using a detecting element include a magnetic tape, a Hall element, a Ci-sensitive diode, and an induction coil.
The detection magnetic field is used to detect the leakage magnetic field: magnetic magnetic flaw detection method, induction coil flaw detection method, Hall element detection method, and magnetic sensitive diode detection method.
Principle of magnetic particle inspection
After the ferromagnetic material and the workpiece are magnetized, due to the discontinuity, the magnetic field lines on the surface of the workpiece and the near surface are locally distorted to generate a leakage magnetic field, and the magnetic powder applied on the surface of the workpiece is adsorbed to form a magnetically visible magnetic field under suitable illumination. Traces, thus showing discontinuous position, shape and size.
Applicability and limitations of magnetic particle inspection
Applicability: Magnetic particle flaw detection is suitable for detecting the surface and near surface of ferromagnetic materials with small size and narrow gap (such as cracks with a length of 0.1 mm and a width of micrometers), and visually difficult to see discontinuities.
Limitations: MT cannot detect austenitic stainless steel materials and welds welded with austenitic stainless steel electrodes, nor can it detect non-magnetic materials such as copper, aluminum, magnesium, and titanium. Shallow scratches on the surface, deeper buried holes, and delamination and folding at an angle of less than 20° to the surface of the workpiece are difficult to find.
-
Sales@hata-ndt.com
-
0086-0371-86172891