The root of the weld is not welded, the root is not fused, the root is concave, and the root is defective.
Cause: The causes of root defects such as incomplete penetration, root unfusion, root recess, and wire are generally caused by improper selection of process parameters or improper thickness of the groove angle or improper operation method.
Prevention: Choosing the right process parameters and groove
Remedy: Grind the defect with an angle grinder, chisel or carbon arc gouging. Before the grinding and cleaning, confirm the position of the weld defect and the stress state of the weld. If necessary, apply external force to change the stress state of the weld; A small window can also be opened with a sander at the symmetrical position of the defect to confirm that the defect is clear. After confirming that there is no defect, repair welding is performed. In special cases, the weld can be cut and re-welded. During the repair welding, the position of the arc starting and extinction arc must be taken into account and the necessary interlayer cleaning should be carried out. After the repair welding is completed, the weld seam should be polished to make the transition smooth.
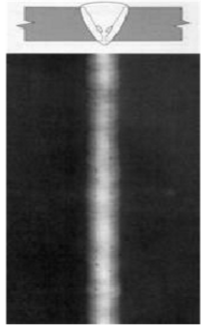
Non-circular defects such as internal cracks in the weld
Reason: The cause of cracks and other non-circular defects is generally due to improper selection of process parameters or failure to meet the requirements of the inter-layer cleaning or welding materials that do not meet the requirements or improper operation methods or the construction environment does not meet the requirements or the workpiece is contaminated with oil and water during the welding process. When the dirt or workpiece is welded, the weld is in a state of strong external force.
Prevention: Corrected from the above items.
Remedy: For the crack of the near root, the strip slag, and the rework of the strip vent should be cleaned by angle grinder, electric motor or carbon arc gouging. Before the cleaning, the position of the welded joint must be confirmed. The weld is reworked under no-stress conditions to prevent cracks from occurring again during the cleaning process; if necessary, an electric drill is used to punch the crack holes. For the penetrating crack, the PT test should be performed after the removal of the weld defect position. After confirming that the defect is eliminated, repair welding can be performed. During the repair welding, it is necessary to take into account the position of the arc starting and extinction arc and carry out the necessary layer cleaning. After the repair welding is completed, the welding seam should be polished to make the transition smooth.
Cutting re-welding
Reason: The weld must be cut and re-welded. Generally, the weld has serious defects such as incomplete penetration, concave, dense pores, or improper selection of welding methods or incorrect installation of the pipeline.
Prevention: Correction from the above projects
Remedy: Use a corner grinder, chainsaw, carbon arc gouging and other tools to segment or treat the weld. When re-welding, the original weld metal shall be removed first; the shape of the groove shall meet the requirements of the welding operation, and the groove shall be repaired if necessary; the welding technical requirements for the re-welding of the cut shall not be lower than the requirements of the original welding process.
Tungsten arc welding root layer tungsten
Prevention: using high frequency arc striking method or erasing method to lead arc, skilled arc striking method
Remedy: Use an angle grinder, electric grinder or welder chisel to clean the defect until it is clear and re-welded.
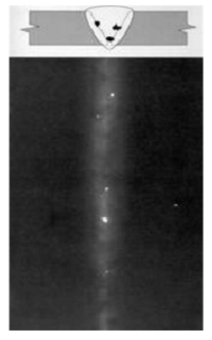
-
Sales@hata-ndt.com
-
+86 371 63217179