Non-destructive testing is to use the characteristics of sound, light, magnetism and electricity to detect the presence or absence of defects or inhomogeneities in the object under test without impairing or affecting the performance of the object to be inspected, and to give the size and location of the defect. The general term for all technical means such as the nature and quantity, and then the technical state of the object to be inspected (such as pass or fail, remaining life, etc.).
Commonly used non-destructive testing methods: ultrasonic testing (UT), magnetic particle testing (MT), liquid penetrant testing (PT) and X-ray testing (RT).
Magnetic particle detection
First, let's take a look at the principle of magnetic particle detection. After the ferromagnetic material and the workpiece are magnetized, due to the discontinuity, the magnetic field lines on the surface of the workpiece and the near surface are locally distorted, and a leakage magnetic field is generated, and the magnetic powder applied on the surface of the workpiece is adsorbed to form a magnetically visible magnetic field under suitable illumination. Traces, showing the location, shape and size of the discontinuities.
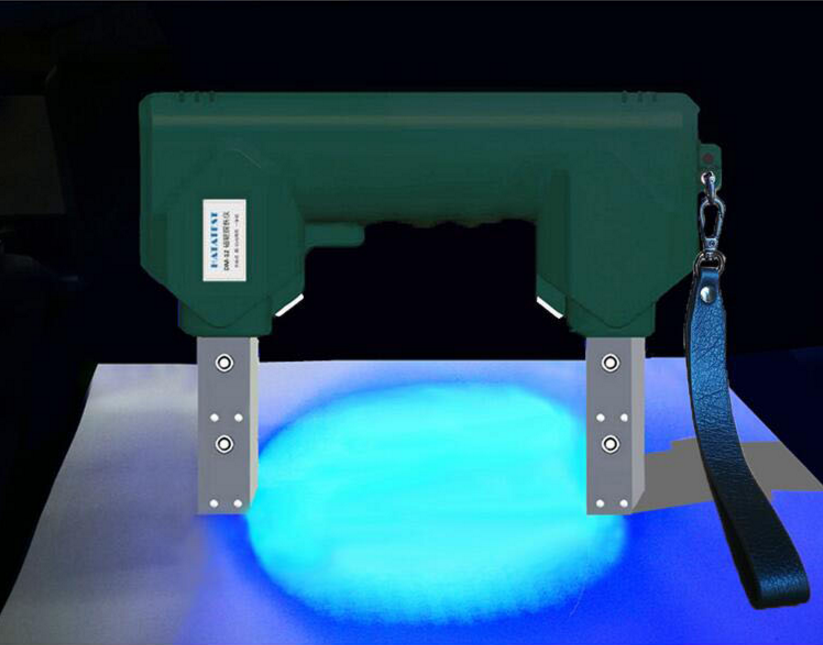
The applicability and limitations of magnetic particle testing are:
1. Magnetic particle inspection is suitable for detecting discontinuities in the surface and near surface of ferromagnetic materials with small dimensions and extremely narrow gaps.
2, magnetic particle testing can detect parts in a variety of situations, and can also be tested in a variety of types.
3, can be found cracks, inclusions, hairline, white spots, folding, cold separation and loose and other defects.
4. Magnetic particle testing cannot detect austenitic stainless steel materials and welds welded with austenitic stainless steel electrodes, nor can it detect non-magnetic materials such as copper, aluminum, magnesium and titanium. It is difficult to find delaminations and folds with shallow scratches on the surface, deeper buried holes, and angles less than 20° to the surface of the workpiece.
Liquid penetration test
The basic principle of liquid permeation detection, after the surface of the part is applied with a fluorescent dye or a coloring dye, the permeate can penetrate into the surface opening defect under the capillary action for a period of time; after removing the excess permeate on the surface of the part, The surface of the part is coated with a developer. Similarly, under the action of the capillary, the developer will attract the permeate retained in the defect, and the permeate will be back-infiltrated into the developer under a certain light source (ultraviolet light or white light). The traces of the permeate are realistic (yellow-green fluorescence or bright red) to detect the morphology and distribution of the defects.
The advantages of penetration testing are:
1. It can detect various materials;
2, with higher sensitivity;
3. The display is intuitive, the operation is convenient, and the detection cost is low.
The disadvantages of penetration testing are:
1. It is not suitable for inspecting workpieces made of porous loose materials and workpieces with rough surfaces;
2. The penetration test can only detect the surface distribution of the defect, and it is difficult to determine the actual depth of the defect, so it is difficult to quantitatively evaluate the defect. The detection result is also greatly affected by the operator.
X-ray inspection
In the last case, the ray detection is because the X-rays have a loss after passing through the object to be irradiated, and different substances of different thickness have different absorption rates for them, and the film is placed on the other side of the object to be irradiated, because the ray intensity is different. By generating the corresponding graphics, the reviewer can judge whether the inside of the object is defective or not, based on the image.

Applicability and limitations of radiography:
1. It is sensitive to the detection of volumetric defects, and it is easier to characterize the defects.
2. The ray film is easy to retain and has traceability.
3. Visually display the shape and type of the defect.
4, the shortcomings can not locate the burial depth of the defect, while the detection thickness is limited, the film needs to be specially sent for washing, and it is harmful to the human body, and the cost is high.
All in all, ultrasonic and X-ray inspection are suitable for inspection of internal defects; among them, ultrasonic waves are suitable for parts with a shape of more than 5 mm, and X-rays cannot locate the buried depth of defects and have radiation. Magnetic powder, penetrant inspection is suitable for inspection
-
Sales@hata-ndt.com
-
+86 371 63217179