Nondestructive testing (NDT) provides the ability to monitor various aspects of material and product quality without compromising part integrity. Many NDT technologies can be applied to ensure proper manufacturing and functionality. Three such techniques—ultrasonics, eddy current and X-ray fluorescence—can be used together in manufacturing operations to ensure use of proper materials, identify near surface cracking and provide volumetric detection of critical defects.
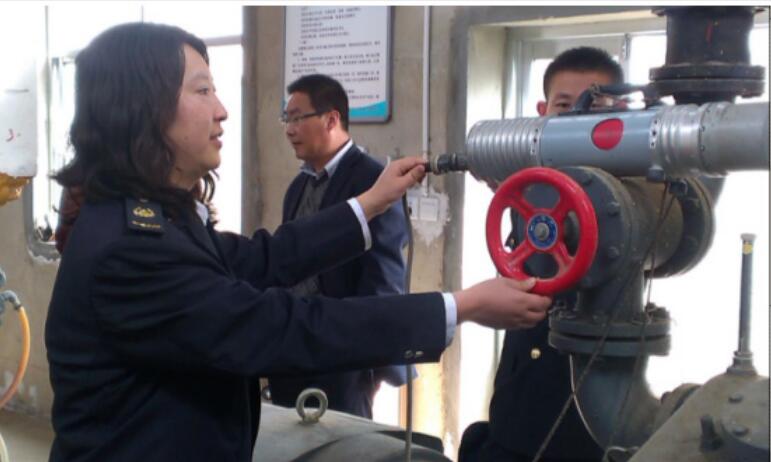
Ultrasonic Testing
Ultrasonic testing (UT) is one of the oldest and most established NDT technologies, having been in wide use since the mid-20th century. UT utilizes pulses of high-frequency sound waves to detect hidden cracks, voids, porosity and other internal discontinuities in metals, composites, plastics and ceramics. Because sound waves travel through materials in predictable ways and reflect off defects and imperfections, like cracks, the internal condition of weldments or other test pieces can be determined by monitoring the pattern of the ultrasonic echoes that UT generates.
Ultrasonic flaw detectors are small, microprocessor-based instruments suitable for use both in the shop and the field. They typically include an ultrasonic pulser/receiver, hardware and software for signal capture and analysis, a waveform display and a data logging module. Traditional flaw detectors provide a waveform display for analysis, while advanced phased array instruments add the ability to generate cross-sectional images of the test piece, similar to medical ultrasound imaging.
Weld inspection is the single most common industrial application for ultrasonic testing. Ultrasonic flaw detection is a comparative technique. Probes, called transducers, generate high-frequency sound waves and are coupled to the test piece through a layer of liquid or gel. A trained operator uses appropriate reference standards along with knowledge of sound wave propagation and generally accepted test procedures to identify specific echo patterns and compare them to the echo patterns produced from intact areas and from representative flaws. Through this process, an operator is able to determine the test piece’s condition. In manufacturing applications, metal and plastic welds and most types of adhesive bonds can be tested.
Eddy Current
Eddy current testing (EC) is based on principles of magnetism. It is widely used in the aerospace industry and other manufacturing applications that require inspection of thin metal for potential safety or quality problems. In addition to detecting cracks in metal sheets, tubes and manufactured parts, eddy current can be used for certain metal thickness measurements such as identifying corrosion under aircraft skin, measuring conductivity, monitoring effects of heat treatment and determining the thickness of nonconductive coatings, like paint, over conductive substrates.
Eddy current testing is based on the physics of electromagnetic induction. In an eddy current probe, an alternating current flows through a wire coil and generates an oscillating magnetic field. If the probe and its magnetic field are brought close to a conductive material, a circular flow of electrons, known as an eddy current, will begin to move through the metal like swirling water in a stream. The flowing eddy current generates its own magnetic field, which interacts with the coil and its field through mutual inductance. Changes in metal thickness or defects like near-surface cracking interrupt or alter the eddy current, resulting in changes of electrical impedance in the coil. The resultant impedance amplitude and phase angle change can be used by a trained operator to identify changes in the test piece.
Since eddy current is best used for detecting surface-breaking cracks, one of its most practical applications is inspecting welded structures that are subject to cyclical loading, which can lead to fatigue crack propagation in critical welded areas. Eddy current inspection of conductive materials offers several benefits over competing inspection techniques. Traditionally, a suspect weld is stripped and cleaned, then a magnetic particle or liquid penetrant inspection is performed to detect any surface-breaking cracks. These techniques have high consumables cost and require pre- and post-inspection cleanup. Magnetic particle testing is not an option for non-ferritic materials like aluminum and stainless steel. Eddy current uses specially designed weld inspection probes incorporating differential coil probes and dual frequency techniques to test rough weld beads through paint or another coating if necessary. Eddy current NDT enables quick inspection of large areas without the use of coupling liquids.
X-ray Fluorescence
X-ray fluorescence (XRF) is based on the interaction of matter with X-rays, which are short-wavelength, high-energy beams of electromagnetic radiation. When a primary X-ray beam strikes a substance, it excites elements at the atomic level, causing electron movement. Each element has characteristic emissions of secondary (fluorescent) X-rays when these movements occur, making it possible to identify the elemental composition of the substance. XRF can identify elements with an atomic number of 12 and up (magnesium through uranium). Unlike other technologies, XRF provides qualitative and quantitative material characterization of metals and alloys. XRF is used for material identification, alloy grading, process control and regulatory compliance, such as ROHS. XRF is used in industries like mining and geology, scrap and recycling, precious metals screening, environmental safety, consumer safety and general manufacturing. XRF operates on a material’s surface with very little penetration.
For weld inspection, handheld XRF instruments have three applications. They can be used for quality assurance of incoming weld material to ensure compliance with ordering specifications. Since weld rods often have a coating of flux, the proper procedure is to make a weld puddle spot and then analyze the spot with XRF. After welding, XRF can perform compositional analysis of the weld and surrounding base metal as a process check, and also to identify deposited weld material after surface treatment like grinding or machining.
Nondestructive testing of welds is an important part of any quality control program. While each of the three technologies described has both strengths and weaknesses, when used together, they provide the most complete assessment of material and weld quality.
-
Sales@hata-ndt.com
-
+86 371 63217179