X-ray inspection is a non-destructive inspection method widely used in many industries because of the non-contact property of X-ray inspection (different from ultrasonic, magnetic inspection method), when certain environmental requirements and the measured object have a specific shape, X Radiation detection is the only viable means of detection. X-ray digital imaging technology has become a mainstream radiation detection technology at home and abroad because of its high-efficiency imaging performance.
At present, there are more standards and requirements for X-ray digital imaging detection technology at home and abroad, which are divided into method and product categories. Some of these requirements are for image quality and for the manufacturing of core components. System integrators and end users will find the basis from the current standard system when it comes to related X-ray digital imaging. However, in the specific case where only X-ray digital imaging technology can be used as the non-destructive testing method, the performance of the image standard and the performance of the digital flat panel detector cannot be effectively matched to the physical characteristics of the object to be inspected. Avoiding cost waste caused by excess performance or failing to meet the expected quality due to insufficient performance becomes a complicated process.
Casting, as an indispensable metal forming method in national production, is quite common in industrial production and daily life. As an important means of quality control, the X-ray digital imaging detection method is one of the non-destructive testing methods available on the market that can match the large-scale production line speed of the manufacturing plant.
In the E03.04 non-destructive testing volume of the ASTM non-destructive testing system in the United States, there are 6 commonly used digital reference map standards and the reference film standard number represented in parentheses:
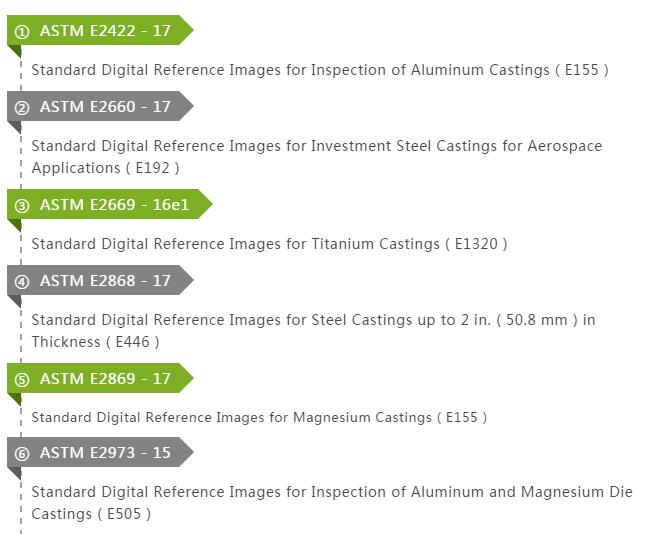
In foreign trade, Chinese foundry companies usually use the materials and thickness specified in the above six standards to meet the quality requirements of foreign sellers when performing quality control on products. After a large number of application verification and image comparisons by system integrators at home and abroad, it is concluded that the image effect of X-ray digital imaging meets the requirements of ASTM standards for acceptance. From the division of defects, defects, the classification of defect categories, the division of defect levels has been accepted by users at home and abroad. In order to meet the requirements of relevant standards, Shanghai HATATEST has designed a variety of flat panel detectors for different scenarios.
When selecting a flat panel detector, you should have a more comprehensive understanding of the casting to be inspected. The material, transillumination thickness, external dimensions, and image standards to be executed will all be expressed in the final image quality. Only after fully understanding the requirements and specific conditions can we have a correct understanding of the choice of flat panel detectors.
-
Sales@hata-ndt.com
-
+86 371 63217179