When we board a train, cross a bridge or enter a shopping mall, we rarely stop to worry whether the structure is sound. Thanks to the inspection industry, we now take safety for granted.
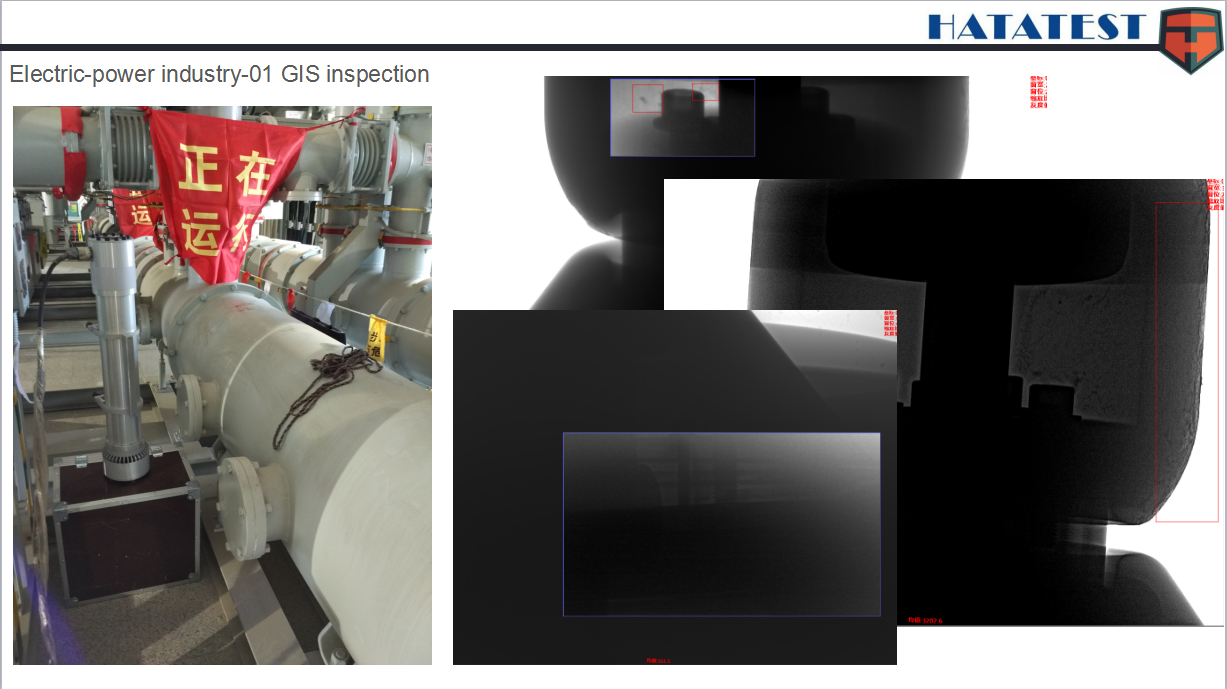
Nondestructive testing (NDT) is the ‘unsung hero’ of the modern world, only coming into the limelight when there is a high-profile failure such as an air crash or a fairground-ride accident.
We all know that it is safer to fly on an aircraft than to cross a road or drive a car, but we have failed to grasp the role that NDT has played in that. While global passenger miles have increased rapidly, fatal accidents have decreased so there is now only one fatality per 8 billion passenger miles. NDT is not solely responsible for the steady improvement in safety, but it is largely the reason that it has been achieved affordably and reasonably delay-free for passengers.
NDT and the associated disciplines of structural health monitoring (SHM) and condition monitoring (CM) not only enhance safety—they can also reduce costs and improve performance. NDT can determine if a component is performing its required structural role through in-service inspections, help prove it at the design stage (certification), ensure manufacturing conformance to design (process control and quality control) and reduce risk to allow more efficient structural designs.
New inspection techniques are opening up new possibilities. The use of CM now allows data from aero engines to be streamed back to a control center while the engine is in flight, enabling early identification of precursors to faults and triggering maintenance in the next airport that is adequately equipped. Similar monitoring is performed on wind turbines.
Looking to the future, NDT will have an even bigger role to play. NDT will make greener air, land and sea travel possible and affordable by increasing confidence in structural design, allowing lighter-weight structures and reducing fuel consumption.
It will also play a central role in the fourth industrial revolution or Industry 4.0. The use of artificial intelligence and machine learning to process big data from the internet of things will lead to the tracking of component life using the ‘digital twin’ concept. One of the principal types of data used will be information from NDT, SHM and CM received via installed sensors.
-
Sales@hata-ndt.com
-
+86 371 63217179