Wind energy is a green renewable energy source with good development prospects. China has huge potential for wind energy development and abundant resources. The total amount of wind energy that can be developed is about 1,000-1500 GW. It can be seen that wind power has the potential to become an important part of the future energy structure. Therefore, the development of wind power generation has also attracted much attention, and fan blades are an important part of wind turbines, and are generally made of glass fiber composite materials. Due to the complexity of their manufacturing processes, defects will inevitably occur during the molding process; in addition, Due to the harshness of the working environment and the complexity and variability of the working conditions, different degrees of damage will occur during operation. At present, non-destructive testing methods for fan blade defects mainly include X-rays and ultrasonic waves. However, each test method has its own advantages and limitations, and there is no perfect standard to specify the applicable stage of the test method.
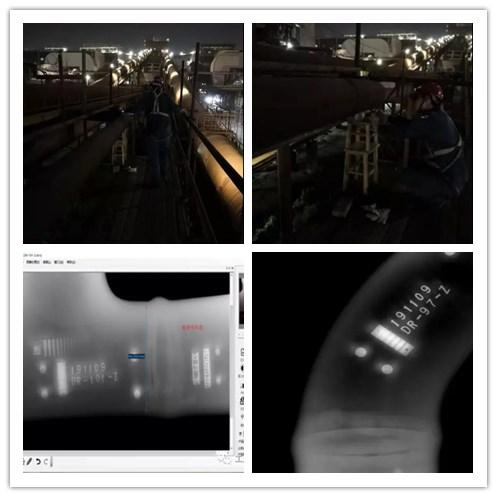
Damage and defect analysis of fan blades
There are many reasons for the defects of fan blades. During the manufacturing process, typical defects such as porosity, delamination and inclusion will occur. Pore defects are mainly caused by poor wetting of resin and fibers, incomplete air displacement, etc .; layering defects are mainly due to insufficient resin consumption, secondary molding, etc .; inclusion defects are mainly due to foreign matter in the processing process.
In addition, during the transportation and installation of the blade, due to the large size and weight of the blade and its elasticity. Therefore, it is important to protect the blades to prevent internal damage. It is worth noting that during the operation of the fan, the blades will also suffer different degrees of damage. The main forms are cracks, fractures and aging of the substrate. External impact is the main cause of cracks. Fractures are usually caused by the accumulation of defect damage. Under normal operating conditions of the fan, the blades will not suddenly break, and the aging of the substrate is due to the long-term operation of the fan blades under the harsh conditions of sand, rain, and salt mist corrosion.
Comparison and Analysis of Nondestructive Testing Methods
For wind power blades, the researchers verified through experiments that X-ray technology is a good method for detecting volume-type defects such as pores and inclusions in wind power blades. It can detect cracks perpendicular to the blade surface and has certain detection capabilities for resin and fiber aggregation. It is also possible to measure defects such as fiber bending in the layup of small-scale wind power blades, but it is not sensitive to the common layering defects and cracks parallel to the blade surface in wind power blades. In the literature, defects such as pores and inclusions were tested. The existence of defects can be observed in the experimental results, which can meet the inspection of the leaves before leaving the factory, and can perform qualitative analysis.
For in-service wind turbine blades, it is difficult to achieve on-site detection using X-ray detection methods due to the influence of field factors and height restrictions. The method has not been widely applied to the full-scale detection of leaves.
Ultrasonic testing technology
Ultrasonic detection technology is more suitable for inspection of fan blades. At this time, the fan blades have not been installed. The purpose of inspection is to ensure the quality of the fan blades. Using ultrasonic detection technology can effectively detect the thickness change and can show the Hidden faults, such as delamination, inclusions, pores, lack of adhesive, and inadequate bonding at the bond, can greatly reduce the risk of blade failure. Due to the obvious anisotropy of the composite structure, the effects of reflection, scattering and attenuation will make the propagation of ultrasonic waves in the multilayer structure of the composite material complicated. The ultrasonic detection methods for the blade structure of the wind turbine mainly include the pulse echo method And air-coupled ultrasonic guided wave method.
Due to the long detection cycle of this method, different specifications of probes are needed for different types of defects, and the use of couplants in the detection process is also a limitation. Therefore, for real-time dynamic monitoring, ultrasonic detection technology is difficult to implement, but static inspection can be performed before leaving the factory. Reflection pulses will be formed in the area where the defect exists, so the location where the defect occurs can be determined.
-
Sales@hata-ndt.com
-
+86 371 63217179