With the development of the times and the advancement of science and technology, higher and higher requirements are placed on the safety status of products, product quality and performance. Due to the superiority of non-destructive testing technology, in the manufacture and use of pressure vessel products. Has been widely used.
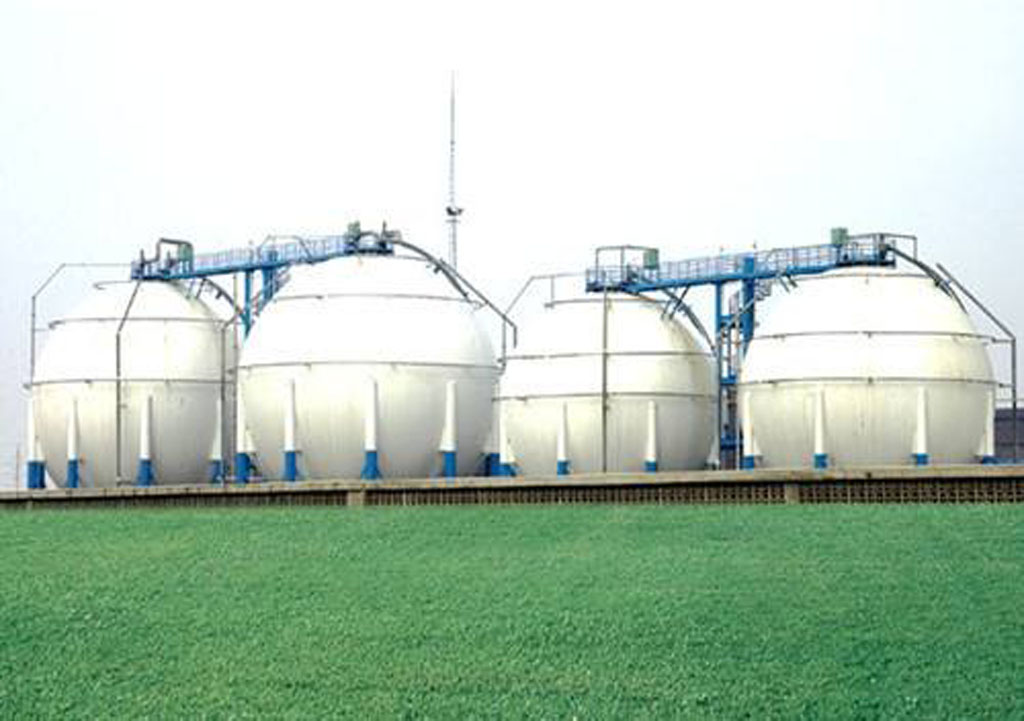
At present, according to the definition of the American Society for Testing and Materials, radiographic testing can be divided into four categories: photogrammetry, trial imaging detection, chromatographic detection and other radiographic techniques. Radiography is the most widely used radiography in pressure vessels. method.
Radiography refers to the penetration of test pieces by X-rays or Y-rays. In the test pieces, the difference in strength due to the presence of defects affecting the washing of the rays, the defects are detected by measuring the difference, and x-ray film is used as a device for recording information. Detection method. Radiographic equipment can be divided into: X-ray machines, high-energy radiation detection equipment, and Y-ray inspection machines.
Characteristics of radiography:
1. Obtain an intuitive image of the defect and locate it accurately.
2. The test results can be recorded directly and can be stored for a long time.
3, the detection rate of volumetric defects (such as pores, slag, etc.) is very high, for area defects (such as cracks, unfused, etc.) such as the photographic angle is not appropriate, easy to miss detection.
4. It is suitable for inspection of butt welds, and the inspection of fillet welds is inferior. It is not suitable for inspection of plates, bars and forgings.
Application characteristics of non-destructive testing on pressure vessels
1. Non-destructive testing should be combined with destructive testing
Non-destructive testing technology has many advantages, but it has its own limitations and cannot replace destructive testing. When evaluating pressure vessel equipment, the non-destructive test results should be compared and verified against the destructive test results to make a correct judgment. For example, liquefied petroleum gas cylinders are subjected to blasting tests in addition to non-destructive testing. In addition to the non-destructive testing, the quality of the welded joints is also to be taken for mechanical analysis, and sometimes metallographic and fracture testing is required.
2. Correctly choose the timing of implementation of non-destructive testing
Non-destructive testing of pressure vessels is based on the purpose of monitoring, combined with equipment operating conditions, materials and manufacturing process characteristics, to correctly select the implementation timing of non-destructive testing. For example, the splicing head should be non-destructively tested after forming; materials with a tendency to delay cracking should be tested at least 24 hours after welding; materials with a tendency to reheat cracking should be added to a non-destructive test after heat treatment; standard tensile strength Low-alloy steel pressure vessels with a lower limit of 540 MPa or higher shall be subjected to surface non-destructive testing of the welded joints after the withstand voltage test.
3. Choose the appropriate non-destructive testing method
When performing non-destructive testing on pressure vessel equipment, all kinds of inspection methods have certain characteristics, and all workpieces and all defects cannot be applied. To improve the reliability of test results, the materials, manufacturing methods, working media, and failure modes of the equipment should be used. And select the type, shape, location and orientation of the defects that may be generated, and select the most suitable non-destructive testing method.
4, comprehensive application of various non-destructive testing methods
In non-destructive testing, it must be recognized that none of the non-destructive testing methods are omnipotent, each with its own advantages and disadvantages. Therefore, in non-destructive testing, if possible, do not use only one non-destructive testing method. Instead, use centralized detection methods as much as possible to complement each other and get more defect information, so as to have a clearer understanding of the actual situation to ensure Safe long-term operation of pressure vessel equipment.
The above briefly introduces several methods and characteristics of non-destructive testing of pressure vessels. In practical applications, we should combine the characteristics of various non-destructive testing methods and select suitable non-destructive testing methods. It is a non-destructive testing technology that can be used in pressure vessel products. Good application.
-
Sales@hata-ndt.com
-
+86 371 63217179