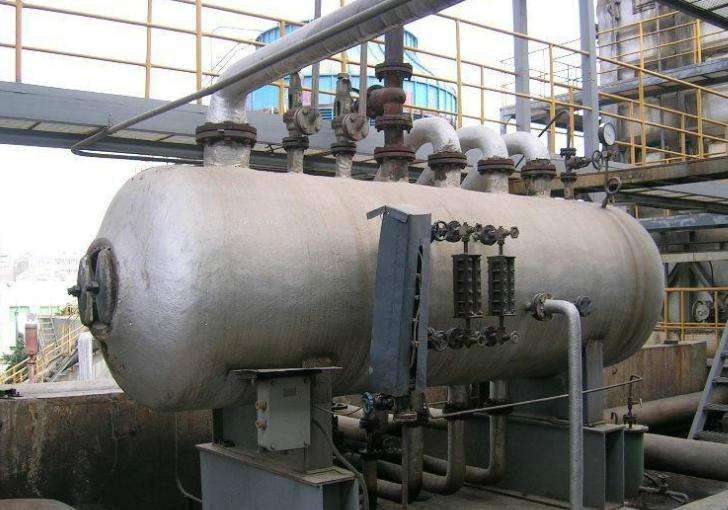
Passing ball test
Deformation of the pipe section due to defects such as welds in the butt weld of the pipe or deformation of the pipe section reduces the flow cross section, thereby affecting the normal operation of the circulation system. Pass the ball test on a tube with a nominal heating surface of ≤ 60 mm.
The ball test is based on the tube with different nominal inner diameters or the ratio of the different bend radius to the nominal outer diameter. The pipe with different diameters is used to pass the ball.
Non-destructive testing of weld surface
In the manufacturing process of industrial boilers, in order to ensure the quality of the weld surface, the weld is usually detected by surface non-destructive testing technology. The main methods are magnetic powder and penetration testing. The general process of the manufacturing unit requires that you perform the above tests on the fillet weld.
Non-destructive testing of welds
Non-destructive testing of welds mainly includes ray and ultrasonic testing
1. Radiation detection
Standards, specifications, and design specifications specify that some weld joints require a certain percentage or 100% of the ray inspection during industrial boiler manufacturing. Such as: the drum, the longitudinal and circumferential welds of the furnace, the ring welds of the pipe, etc.
The use of film imaging systems is most common for the barrel, the longitudinal direction of the furnace, the circumferential welds, and the tube girth welds made by some small-scale industrial boiler manufacturers. The use of real-time imaging systems for a large number of pipe ring weld ray inspections is an efficient and economical method.
2. Ultrasonic testing
Standards and specifications stipulate that some welding joints require a certain proportion or 100% ultrasonic testing during industrial boiler manufacturing. Such as the drum, the longitudinal and circumferential welds of the furnace, the girth weld of the pipe, the T-shaped weld of the tube and shell or the furnace or the combustion chamber. In the ultrasonic testing of these welds, the inspection of butt welds of small diameter thin wall pipes is difficult. Since the tube belongs to a thin-walled member with a large curvature, it is required to use a probe with a short front edge, a narrow pulse, and a large incident angle to ensure that one sound wave can scan the root of the inner wall on the other side of the weld. The detection method is based on the center line of the weld, and the presence or absence of defects is determined by the position of the echo in the weld and the intersection, phase and phase of the echo.
-
Sales@hata-ndt.com
-
+86 371 63217179