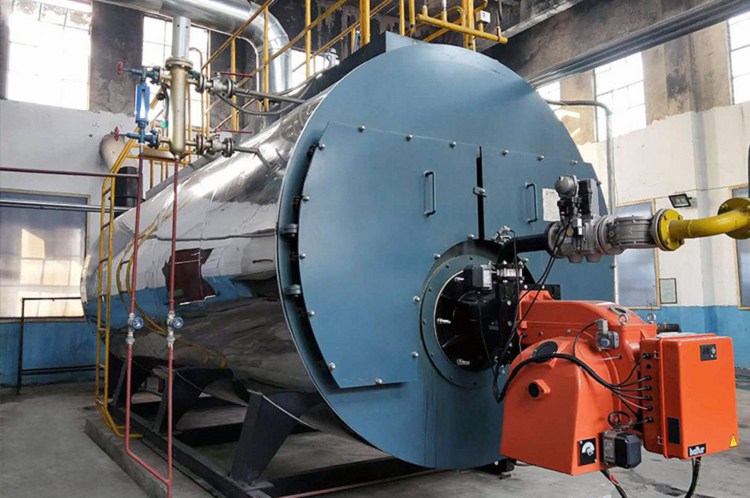
Non-destructive testing during installation
Many products in industrial boilers are manufactured after the final assembly. The on-site installation is to connect the boiler body to the entire system pipeline and control system installation. Other industrial boiler bodies are assembled on site by prefabricated component units from the manufacturer. On-site assembly of welds must first be carried out for surface quality inspection. After inspection, non-destructive testing is carried out according to specifications, design technical conditions and installation process requirements.
X-ray inspection and ultrasonic inspection are often used to ensure a high detection ratio due to the limitation of the position welding position on site. The detection method is the same as that in the manufacturing process.
Non-destructive testing during use
Industrial boilers are subject to periodic inspections during use. The periodic inspection work is divided into external inspection, internal inspection and hydraulic pressure test, which are generally carried out every year, every two years and every six years. When the three are carried out at the same time, internal inspection, hydrostatic test and external inspection should be carried out in sequence. Only when all three are within the validity period, the boiler can be put into use. In the regular inspection process, commonly used non-destructive testing techniques often use electromagnetic eddy current surface crack detection technology in addition to common visual inspection, thickness measurement, hardness measurement, magnetic particle inspection, penetration inspection, ultrasonic inspection and radiation detection.
Visual inspection
Visual inspection is very important in the periodic inspection of boilers. Its main purpose is to check the changes in the body of the boiler after a period of operation. The main content is to check whether the pressure parts of the boiler are cracked, overheated, deformed, leaked, corroded and damaged, whether the boiler expansion system is effective, the heat insulation status of the boiler insulation and refractory bricks, and the use status of the safety accessories. Some effective tools are often used in the inspection. If using the endoscope to observe the box, the internal corrosion and scaling of the pipe fittings, use the hammering method to judge the thinning and cracking of the pressed parts, use a magnifying glass to observe the surface condition of the pressed parts closely, and observe the deformation of the pipe using the flashlight light column. And measuring the amount of deformation of the pressure-receiving member using a measuring tool.
Surface inspection
The surface inspection method is the preferred non-destructive testing method for the complete inspection of the boiler. The surface inspection is the butt weld of the drum and the fillet weld. The surface inspection of butt welds generally uses the magnetic particle detection method. Because the internal lighting conditions of the boiler are not good, the fluorescent magnetic powder detection method is usually used, and the penetration weld method is also adopted when the fillet weld cannot be performed by the magnetic powder test.
-
Sales@hata-ndt.com
-
+86 371 63217179