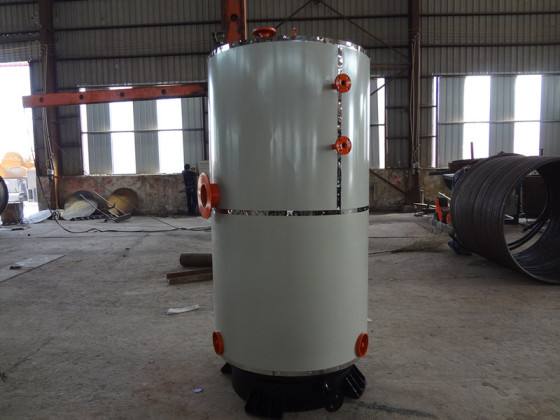
A boiler is an energy conversion device that converts fuel into combustion or electrical energy to release heat in a furnace. The working fluid in the furnace absorbs heat to form steam, hot water or postal heat carrier with a certain temperature and pressure for power generation, production or life. Used on. Boilers are divided into industrial boilers, small boilers and power station boilers according to their use. Industrial boilers generally refer to boilers with a rated working pressure of ≤2.5 MPa, mainly for supplying steam, hot water or organic heat carriers for production or living.
1. Non-destructive testing during manufacturing
The industrial boiler body consists of welding or expansion of the main compression parts. The pressure components of the water tube boiler include a drum, a header, a down pipe, a water wall, a water tube bundle, a slag prevention tube, a superheater, and an economizer. The pressure parts of the boiler shell boiler have a shell, a furnace, a back combustion chamber, a smoke pipe, a sky tube and a lower leg ring. Metal materials for pressure parts include steel sheets, steel pipes, forgings, steel castings, cast iron parts, and fasteners. These pressure parts and raw materials must be non-destructively tested in accordance with the design documents, national and industry standards during the manufacturing process.
2. Visual inspection
In order to ensure the quality of the products, from the purchase of raw materials, the processing of pressure parts, the assembly of parts to the final assembly, the product status should be visually inspected at each stage.
The metal materials used to manufacture the boilers shall be sampled in batches for surface quality and geometrical dimensions. It should also comply with the corresponding standards and the requirements of the order contract.
The geometry, surface quality and opening position of the pressure-bearing components shall be in accordance with the design drawings, standards and process documentation.
All welds of pressure-receiving parts, including joint welds of non-compressed parts and pressure-receiving parts, shall be visually inspected. The dimensions of the weld shall be in accordance with the design drawings and the technical documents. The weld height shall not be lower than the surface of the base metal, and the weld and the base metal shall be smoothly transitioned. Surface defects such as cracks, slag inclusions, craters and pores should not exist on the surface of the weld and heat affected zone. Some under-welded parts are not allowed to have undercuts, and the welds that allow undercuts must not exceed the depth and length. Weld joints shall be of full penetration type, lap joints are not allowed, and T joints are not allowed in some parts. The weld location should also comply with the standard.
-
Sales@hata-ndt.com
-
+86 371 63217179