A conveyor belt is the carrying medium of a belt conveyor system which is widely used across many industrial branches, especially in mining industries for bulk handling of raw materials like coal, coke, iron ore etc. The operation of conveyor belts is closely connected to various kinds of mechanical loading, which causes wear or gradual degradation of the conveyor belts. One of many symptoms indicating such wear and tear is the abrasion of the carrying and of the pulley cover.
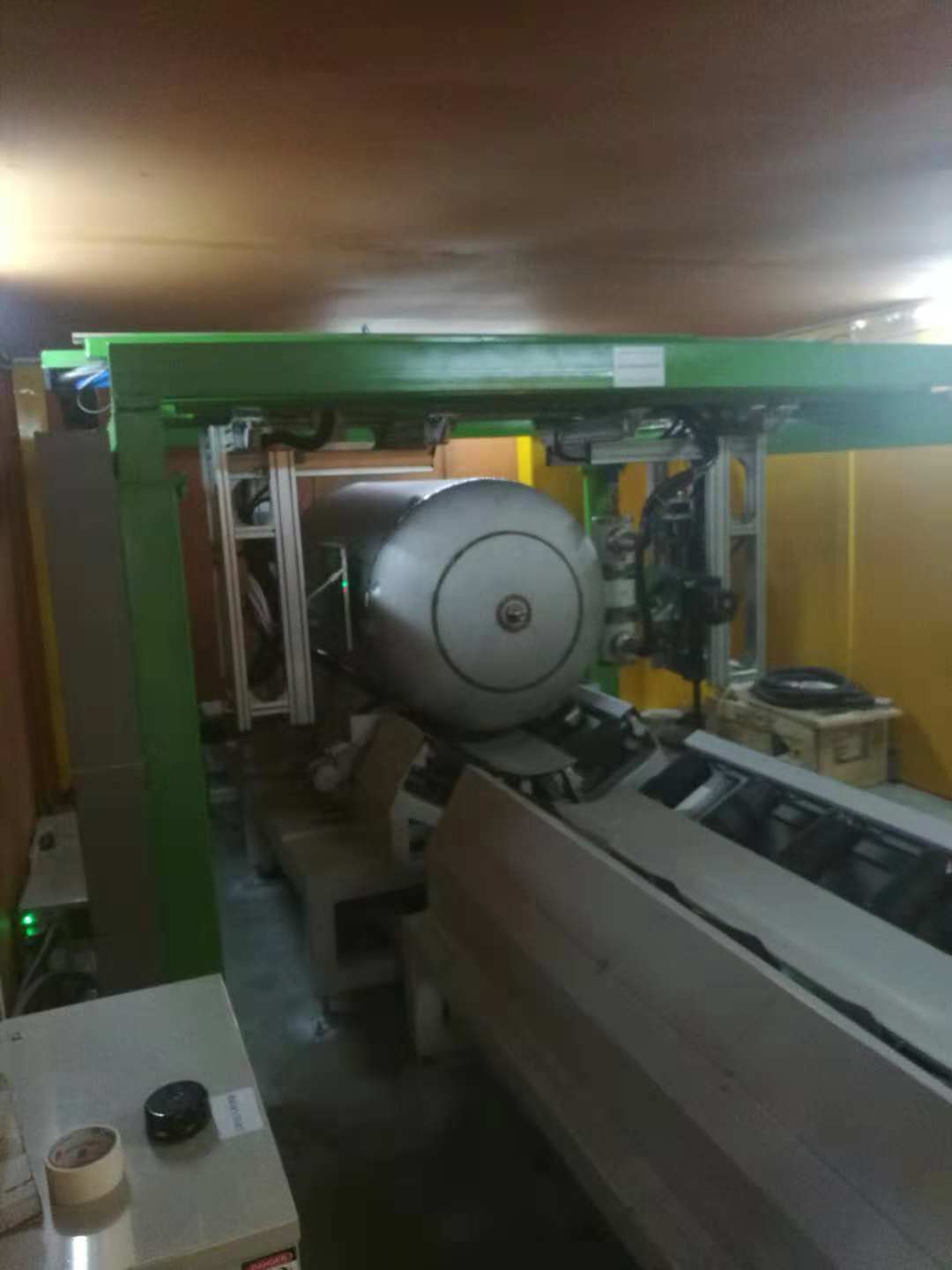
Decrements in the belt‘s cross-section reduce its puncture resistance, thus increasing the risk of core damage. A failure of the rubber belt in conveyor systems can lead to unexpected downtime of the plant and poses high safety risks.
The primary purpose of thickness measurements is to determine the trended wear pattern and rate of wear for reinforced rubber belts. This maximizes the life of the rubber belt by predicting the end of its lifespan providing a tool for effective maintenance as well as allowing belt changes to be incorporated into the relevant budget cycle.
Rubber is a very sound attenuating material. Obtaining two clear back wall echoes is in most cases not possible. Accordingly using the pulse echo technique is recommended. For this reason, the equipment has to be set to single echo mode. SONOTEC recommends dual element probes. In this case, it is important to set up a V-path error correction curve for the probe used during the measurements.
Conveyor belt rubber is usually unique and may vary from belt to belt, it is necessary to calibrate the sound velocity using a sample of known thickness(-es) of the exact rubber which needs to be inspected. Ideally, a two-point calibration is performed which requires two reference thickness of the same material. If this requirement cannot be fulfilled the suggested approach is to zero the probe and using a one point calibration. The sound velocity of typical rubber used for conveyor belts should be around 1650 m/s. If a sample is not available, V-path error correction, probe zero procedure and a manual adjustment of the sound velocity is the recommended approach.
Measurement of the rubber above the reinforcement fabric (top cover) is relatively easy. Fabric is oriented perpendicular to the ultrasonic beam propagation and has a significant acoustic impedance mismatch. The amplitude signal in most cases will be much stronger and easier to evaluate than the back wall echo.
Conveyor belts that consist of steel cords are rather harder to inspect. The cords are not placed over the whole area. One of the difficulties is to locate them by observing the amplitudes that appearbefore the expected back wall echo. The second difficulty would be the round shape of the cord which is not an ideal reflector.
In addition, it can be observed that, due to its composition, the actual reflection point from the cord is actually a bit deeper than the cord tip. It has to be taken into consideration that the remaining rubber thickness is based on the steel cord reflection measurement.
-
Sales@hata-ndt.com
-
+86 371 63217179