After a weld is welded, the appearance quality can be observed and measured. However, the internal weld of the weld can be found by radiographic inspection, such as: porosity, inclusions, cracks, unfused and other defects.
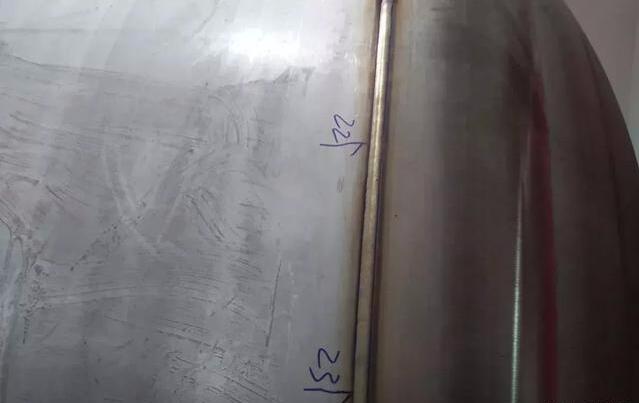
The principle of ray detection is to use X-ray or gamma light source to penetrate the weld and chemically react with the sensitizer (silver bromide) on the film to form a photosensitive factor.
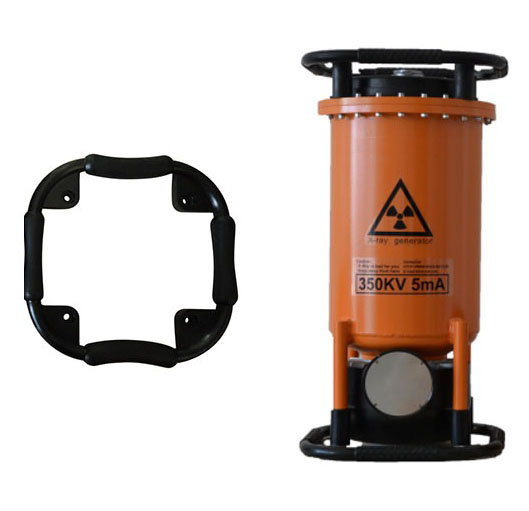
Then, development and fixing of the developer and the fixing solution are successively performed to form an image on the film, and the defect is judged based on the local blackness change of the image. The internal quality inspection image of the weld is tested by this method.
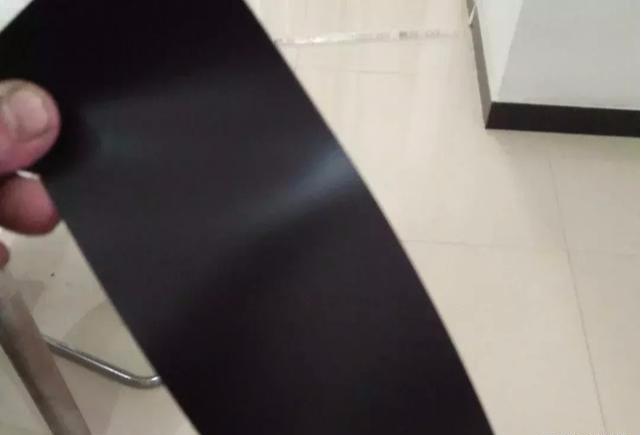
Since there are many steps in the radiation inspection, we have to perform the first step of the appearance of the weld after the welding is completed.
The surface quality (including the residual height) within 50mm of the weld and its edge shall be tested after passing the visual inspection, and may be used to cover up defects or defects, such as craters, depressions and deep welds. The weld bead groove (during multi-pass welding), highly prominent welding waves, splashes, slag, severe mechanical damage and other foreign objects should be eliminated and repaired. If the inspection personnel find that the appearance of the weld is unqualified, the inspection personnel shall promptly notify the on-site supervision and processing before proceeding to filming.
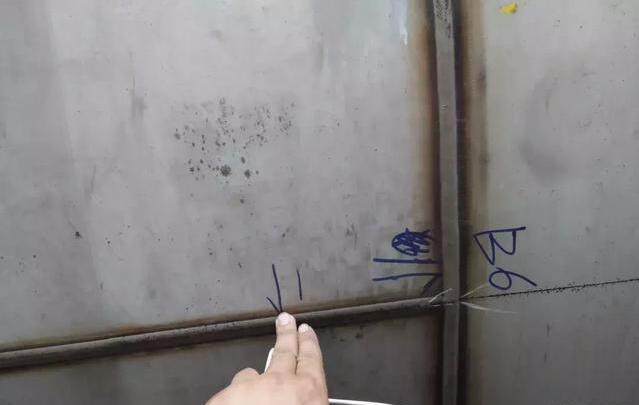
In the weld bead and its heat-affected zone, defects such as cracks and pores are not allowed on the surface. The dimensions of the weld are in accordance with technical standards and design requirements, and the weld and the base metal should be smoothly transitioned.
When the external defect processing is finished, we need to fill in the corresponding entrusted inspection documents to declare.
1. Due to the extremely dangerous radiological safety accidents, the radiation inspection is carried out in a fully enclosed reinforced building, and the access of the equipment welds is separated by a thick anti-radiation isolation door.
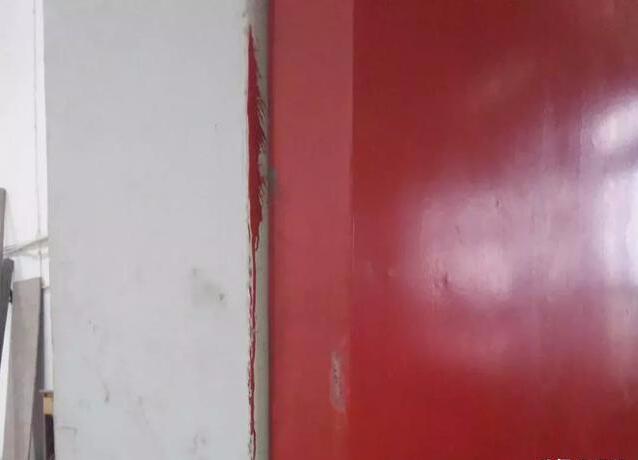
After the device enters, the weld is positioned first, and the dimensions are divided according to the circumference and the length of the ray film.
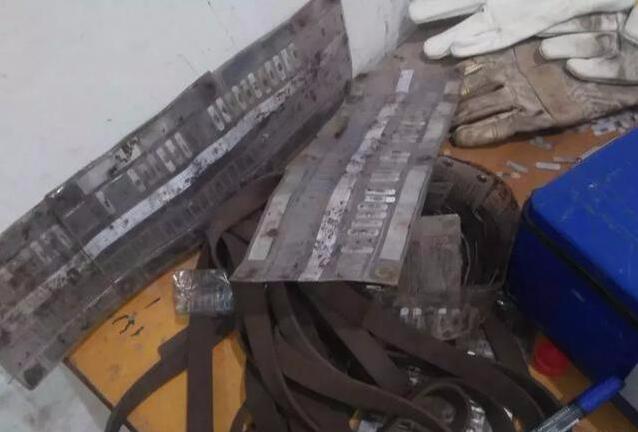
2. After the positioning is completed, the numerical serial number and the overlapping symbol on the available mark of the weld bead.
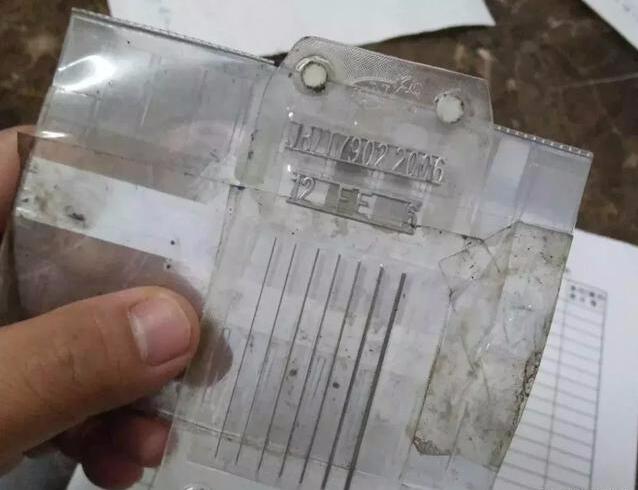
The engineering number, image quality meter, welding port number, and welding method of each film are pressed in the order, and then attached to the corresponding weld arrow position.
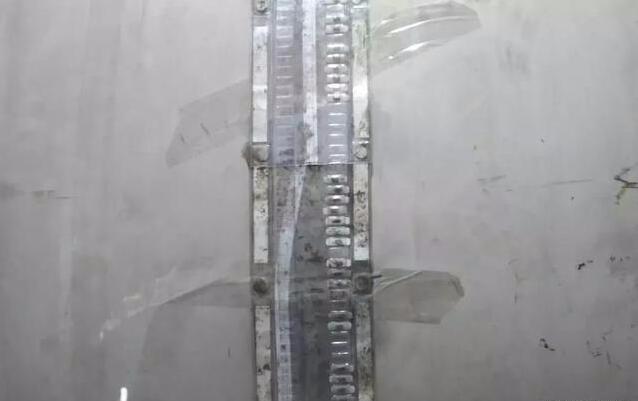
In order to make each ray film and the workpiece to be inspected at all times, the lead identification mark and the tested area are simultaneously exposed on the film during the transillumination process. All markings can be glued (or scotch tape) to the strip of transparent transparent base or transparent plastic that is hollowed out to form a marker tape.
3. The important X-ray transmitter should be placed in the center of the weld for a ring illumination, and the placement must be close to the center.
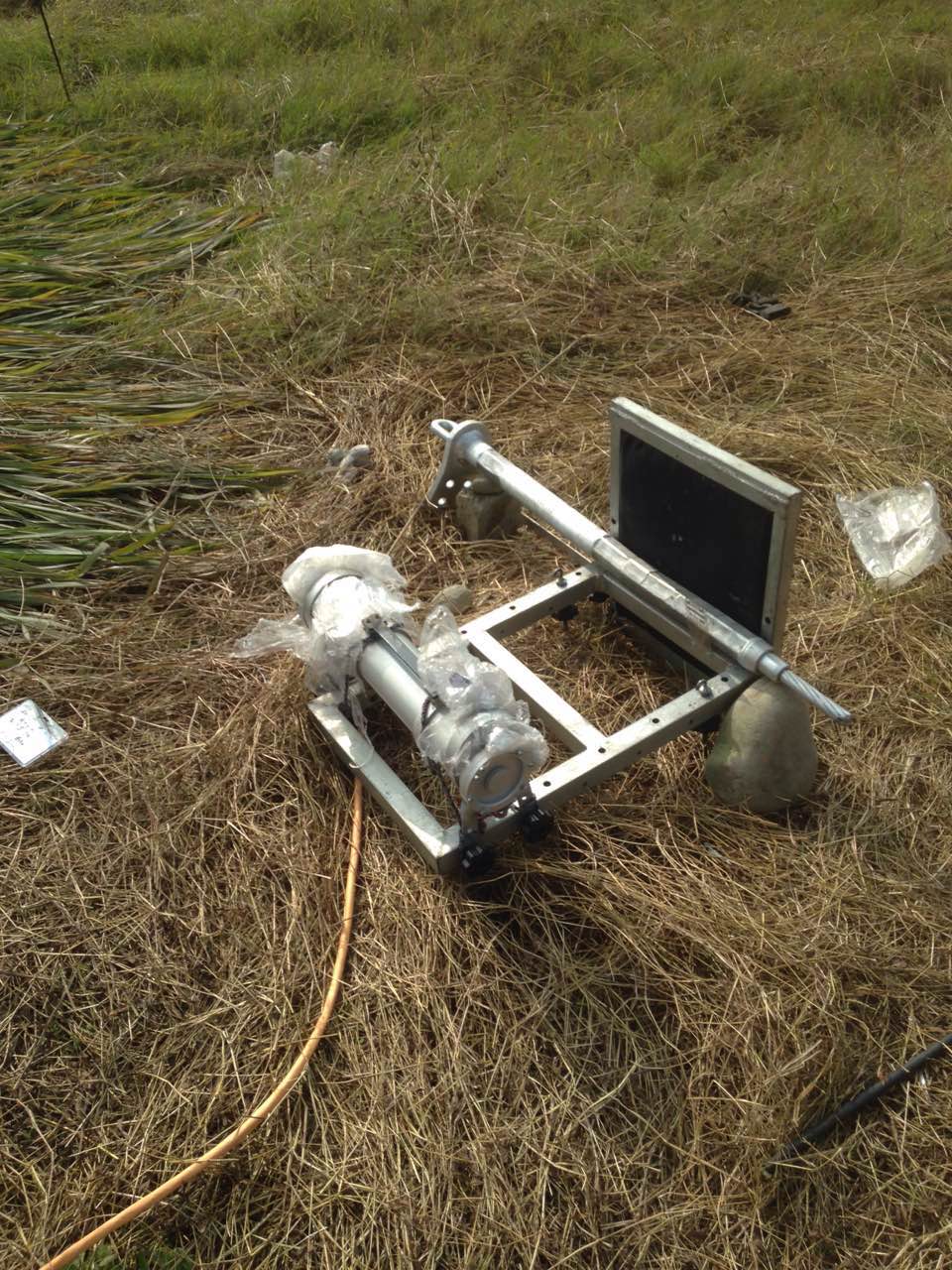
The machine can be calibrated before starting the equipment and the parameters are adjusted according to the thickness of the weld. Industrial film uses Kodak or similarly imaged photosensitive sheets as a pattern. After the film is opened, cut 100 mm, and the background fog is measured after rinsing.
The starting device must be isolated from the human body, and should not be close to the radiation distance of 50 meters. The wall should be thickened as a shield in the closed building.
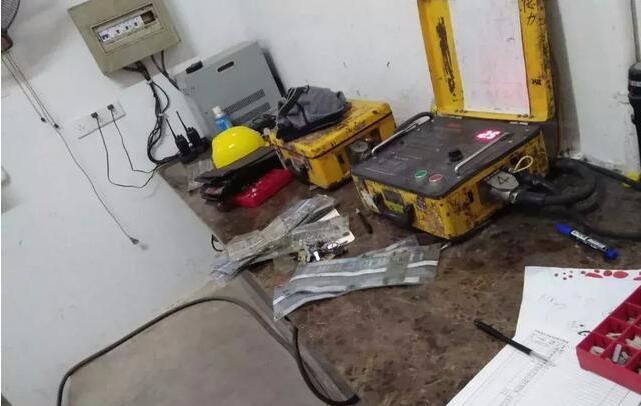
4. After the exposure starts, the exposure time is adjusted according to the weld parameters, and the sheet is over 2 minutes after the end of one exposure. After the X-ray machine is irradiated, the cooling state can be performed to take the film.
5. After the end of the irradiation, the negative film should enter the dark room for cleaning and development. The film is taken out and placed in a fixing solution for styling, and then washed and dried. The welder is evaluated by the reviewer after drying.
The assessment is based on the qualified level, and the first grade is qualified, the second grade is qualified, and the third grade is qualified. The number of films is 20% and 100%.
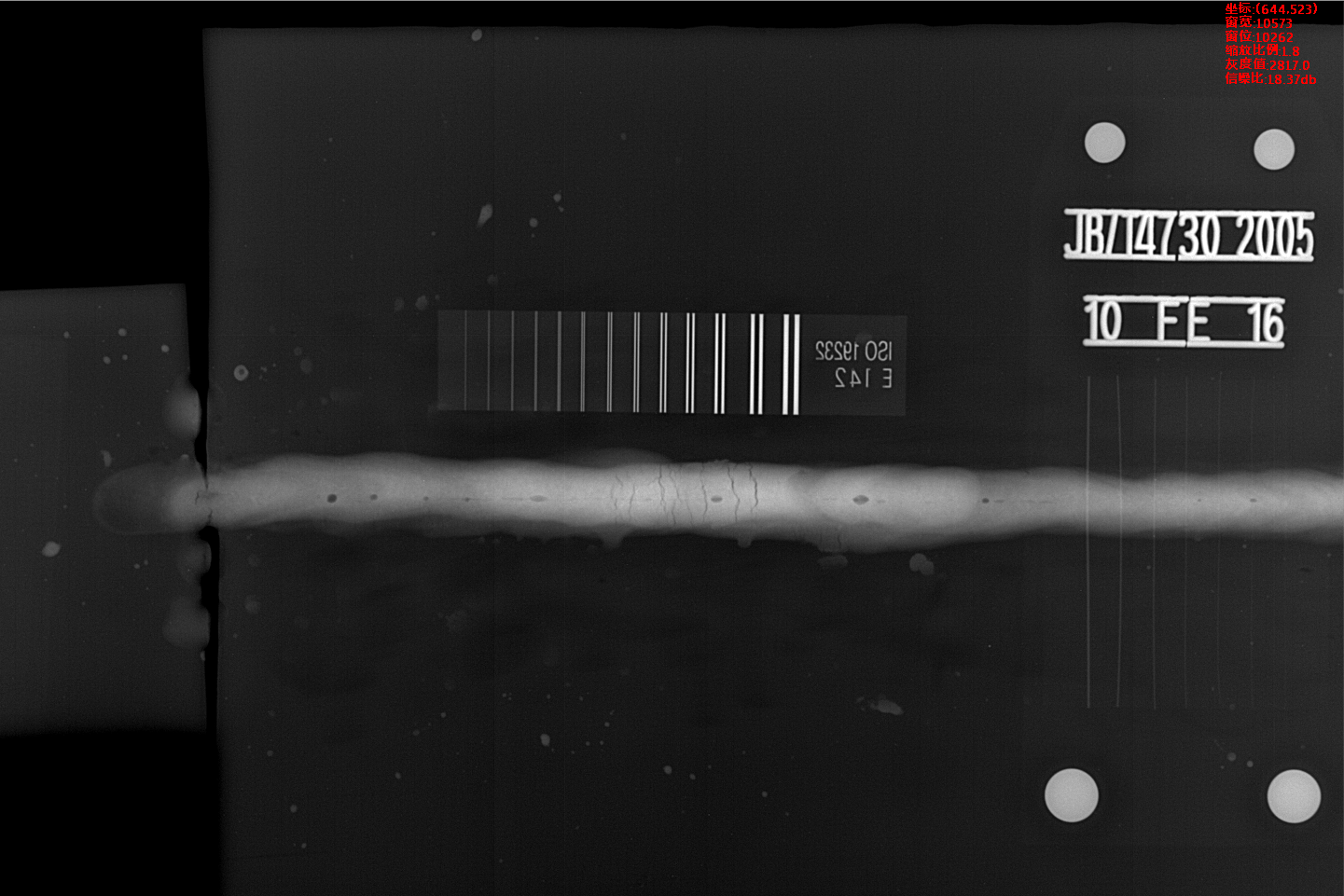
In case of failure to pass the review, it is necessary to carry out the repair process until the seam is sealed. Below is a view of the X-ray defect of the full argon weld. This is the internal primer unfused defect of the full argon weld.
-
Sales@hata-ndt.com
-
+86 371 63217179