X-ray non-destructive testing technology and its application in the detection of refractory products
In the production time and quality inspection of refractory products, destructive testing is usually used. At the same time as the test is completed, the sample is also destroyed, and a destructive test can only be carried out for sampling inspection. The non-destructive testing technology detects the product without damaging the product and structure, and can perform 100% inspection on the product, and can detect small defects inside the sample that cannot be seen by the naked eye.
The continuous casting refractories used in the steel industry, such as forbidden nozzles, integral stoppers and long nozzles, are important functional materials. They are extremely harsh in use and must withstand high temperature molten steel erosion, erosion and cold during use. The thermal shock effect of alternating heat must be guaranteed to be foolproof. After non-destructive testing of functional materials, the detection rate of the product can reach 100%, thus ensuring the stability and reliability of the product quality.
Principles and characteristics of X-ray nondestructive testing technology
1. X-ray machine construction
The X-ray machine used in industrial ray inspection is mainly composed of four parts: a ray generator (X-ray tube), a control system, a high voltage generator, and a cooling system. The core part of the X-ray machine is an X-ray tube and an X-ray tube structure
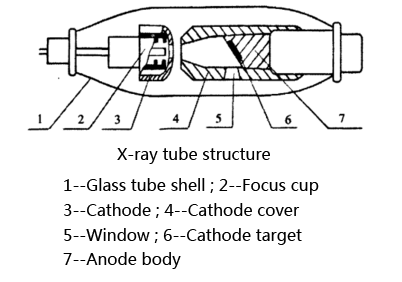
2. Basic principles and sensitivity of X-ray photography technology
The attenuation of the intensity of a ray as it penetrates an object is related to the nature of the absorber, its thickness, and the energy of the ray photons. For a single-color, narrow-beam ray, in a uniform medium of very small thickness, the degree of attenuation of the ray as it passes through the object is exponentially related to the thickness of the object being penetrated. as the picture shows
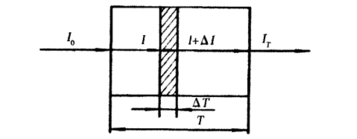
According to the attenuation law of the ray, when the ray passes through the object, the object will absorb the ray. Since different substances have different absorption effects on the rays, images of different blackness will be formed on the film as shown in the figure.
The ability of radiographic detection of defects depends on the contrast, unsharpness and granularity of the radiographic image quality. However, in daily radiographic inspection work, the contrast, unsharpness and granularity of radiographic images are not directly measured, but the concept of radiographic sensitivity is widely used to describe photo records. Radiographic sensitivity is divided into absolute sensitivity and relative sensitivity.
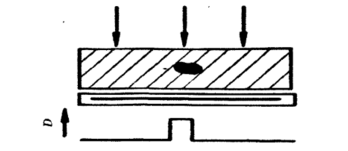
Absolute sensitivity refers to the size of the smallest defect that can be found when a ray is transmitted through a workpiece. When B-level photography is specified in GB3323--87, when the thickness of the base material is ≤3mm, the steel wire with φ0.1mm should be recognized. This is the absolute sensitivity. Notation. The relative sensitivity K is expressed as a percentage of the minimum thickness dimension ΔD at which the defect can be found in the transillumination direction and the penetration thickness d at that point, that is, K = Δd * 100% / d.
-
Sales@hata-ndt.com
-
+86 371 63217179